Reasons for Low Efficiencies of Thermal Power Plants and Ways of Improving It
Electric energy is an essential ingredient for the industrial and all-round development of any country. It is the most sought-after form of energy because it can be generated centrally in bulk and transmitted economically over long distances to the consumers.
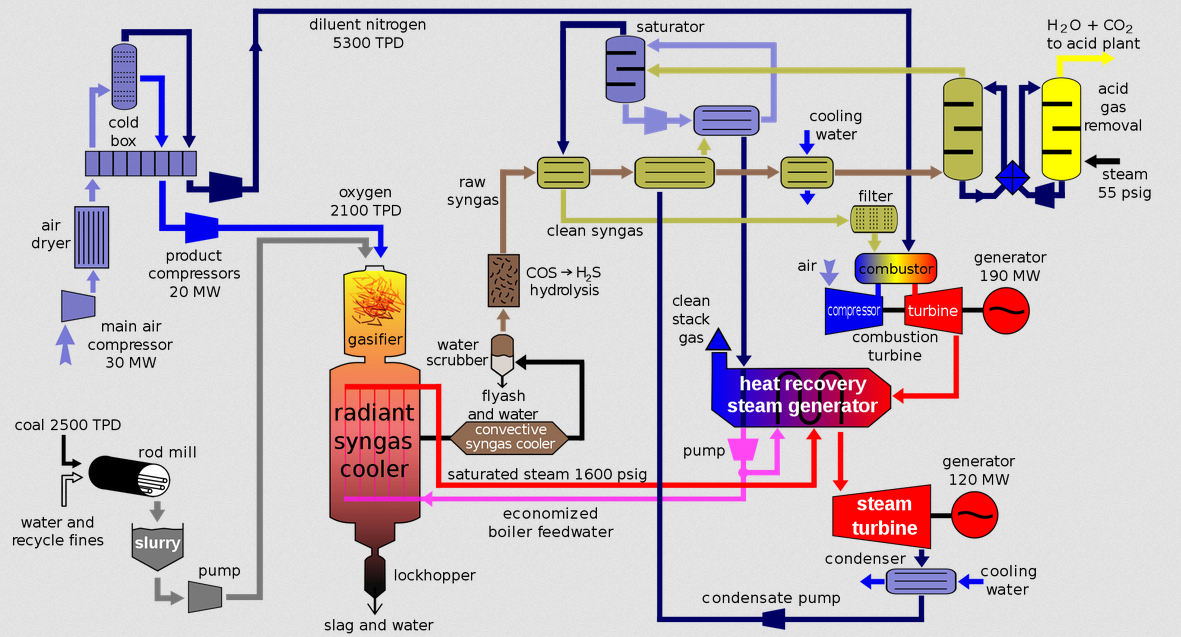.png)
Most often, we refer fossil-fuel plants as thermal power plants, and they produce electrical energy from the heat released by the combustion of fossil fuels. Fossil fuels are of plant or animal origin and consist of hydrogen and carbon (hydrocarbon) compounds. The most common fossil fuels are coal, oil and natural gas. The less common ones include peat, oil shale, biomass etc. Fossil-fuel electric power generation uses the combustion of heat energy from these fuels to produce electricity.
A steam power plant is designed to operate on the Rankine cycle. We can categorise steam power stations into two, namely;
- Condensation power plant and
- Thermoelectric power plants
The condensation power plants are solely intended for the generation of electric energy. Condensation power plants which operate on organic fuels are mostly built near fuel fields to minimise the cost of fuel transportation. They are provided with steam turbines having a high vacuum in the condensers.
Lower pressure of steam off the turbine outlet enhances the transformation of thermal energy in the working fluid into electricity. The majority of the steam is condensed in the condenser and the principal part of heat contained in the steam is lost with the cooling water.
Cogeneration
In the thermo-electrical power plants both heat and electric energy are produced. Such station are usually built near heat load industrial enterprises or large residential districts to supply them with heat.
Thermal power plants for combined generation of electric energy and heat are provided with steam turbines with intermediate steam extractions or with back pressure turbines.
When you look at the enormous amount of waste heat produced in thermal power generation, one will understand the need to save energy by the simultaneous generation of electricity and steam (or hot water) for industrial use and space heating. This is known as cogeneration and efficiencies of up to 65% has been reported.
There are two possible ways of generating both heat and electricity from the same steam plant: (i) Topping cycle, (ii) Bottoming cycle. In the topping cycle, fuel is burnt to produce electrical or mechanical power, and the waste heat from the power generation provides the process heat. In the bottoming cycle, fuel is burnt to first produce process heat and the waste heat from the processes is then used to generate power.
In such plants, the heat of worked off steam is recoverable and is utilised partially or entirely for heat supplies for industrial users and domestic purposes so that the loss of heat in cooling water is largely reduced or even eliminated in the back pressure turbine.
On the other hand, the fraction of heat transformed into electric energy in plants with heat producing turbines is naturally lower than that of the condensation power plants.
The pulverised coal burns and the heat of combustion are used to raised steam in the boiler. The steam is superheated from the extracts of heat from flue gases before it is passed through a regulating valve to the steam turbine where it expands to relinquish heat energy to the steam turbine. The heat energy is converted by the steam turbine to mechanical energy before exhausting the used steam to the condenser where it condenses to water to be fed again to the turbine
Thermal Power Stations
The heat released during the combustion of coal, oil or gas is used in a boiler to raise steam. In Nigeria, heat generation is mostly by coal or oil based. The chemical energy inherent in coal is transformed into electric energy in thermal power plants.
The heat released by the combustion of coal produces steam in a boiler at high temperature and pressure, which when passed through the turbine expands and gives off some of the internal energy as mechanical energy. It is possible to use an axial-flow type of turbine consisting of many cylinders mounted on the same shaft. The steam turbine acts as a prime mover and drives the electric generator (alternator). A simple schematic diagram of a coal-fired thermal plant is shown in the figure below.
Steam power plants could be built with a condenser or without a condenser. In the condensing type power plants, the exhaust steam is discharged into the condenser, which allows the steam to expand to very low pressure, thereby increasing the efficiency.
In the non-condensing type power plants, the steam discharged from the turbine is at atmospheric pressure or a pressure slightly higher than atmospheric pressure.
The condensing type comes with two significant advantages in that greater amount energy is derivable per kg of steam. Thus a more considerable amount of power can be gotten from a given size of turbine or engine. Also since the steam condenses in the condenser, it can be recycled and recirculated to the boiler with the help of the pump.
This recycling of water is especially important in areas devoid of large bodies of water, quite unlike in the non-condensing type which discharges the steam to the atmosphere and as such requires a fresh supply of water pumped into the boiler from a nearby stream or river.’
The Efficiency of Steam Power Station
To appreciate why the efficiency of steam power plants is low, we must consider the laws of thermodynamics. Let us consider a conventional steam engine where the steam forces its way out of a boiler as a result of the existence of temperature and pressure gradient between the engine and the surrounding environment, that is, there is lower temperature/pressure in the ambient environment as compared to the confines of the engine.
It is the pressure gradient throughout the system that ensures steam flow and hence energy is derived as a result of it. It then means that some steam at temperature higher than ambient temperature must leave the system, which means some heat energy is lost.
Let us start with Carnot cycle. We are aware that the Carnot cycle thermal efficiency is less than one despite the fact that it is an ideal system. Why is it so?
The efficiency of up to 100% is achievable if sink temp is 0 Kelvin. The main problem is that our ambient temperature is nearly at 300 Kelvin, so we have to reject heat to this temperature. But as ambient temperature goes down our efficiency goes up, i.e., more heat is converted into work.If the ambient temperature is reduced to 0 Kelvin, it then means that the whole heat can be converted into work. As we have no control over ambient temperature, it is not practical to convert heat into an equivalent amount of work.
The lost of heat is the main reason our power plant efficiency is almost pegged at 45 percent.
A tremendous amount of heat is lost in the condenser, and there is no way to avoid it based on the above explanation. There must exist a temperature difference between the temperature of the steam turbine and that of the exhaust of the condenser for heat energy to be converted into mechanical energy. Greater heat energy will be converted if there exists a broader margin of temperature difference. Better conversion can be achieved in two ways, either by increasing the temperature of the upper reservoir or decreasing that of the lower reservoir.
Unfortunately, there is a limit to which we can raise the temperature of the upper reservoir, and technical reasons place this limit due to the strength of the material used in the construction of the turbine. That of the lower reservoir is governed by the ambient temperature of which we have little control over as explained above. We can also deduce from the explanation above that the higher the temperature difference, the more significant the amount of heat that will be lost.
There is also heat losses at various stages of the system which include heat losses in ash, radiation, flue gases, condenser and alternator. The efficiency of some modern power plants is around 29%. It, therefore, means that if 100 calories of heat are derivable from the combustion of a certain quantity of coal, it means that 29% calories of electrical output are available.
The thermal efficiency of steam power plants depends on the temperature and pressure of the steam entering the turbine. This is why we adopt high temperature and pressure of steam entering the turbine to increase the thermal efficiency. On the other hand, the thermal efficiency increases with a decrease in temperature and pressure of steam in the condenser.
Gas Turbine Power Plants
A typical gas power plant schematic is shown below. Air is drawn through the air intake system into the compressor from the atmosphere. The compressed air is mixed with natural gas and is burnt in the combustion chamber. The products of the combustion (hot and high-pressure air) are then passed to the gas turbine where it is allowed to expand, and the mechanical work produced drives the alternator which generates electricity.
The overall efficiency of gas turbine power plant is somewhat low at about 20% owing to the substantial quantity of heat in the exhaust gas.
Fortunately, there is a way out which involves utilising the exhaust gas from the turbine which still possesses sufficient heat to raise steam which can run a conventional steam turbine coupled to a generator.
This is arrangement is called combined-cycle gas-turbine (CCGT) plant. The schematic diagram of the CCGT is as shown below.
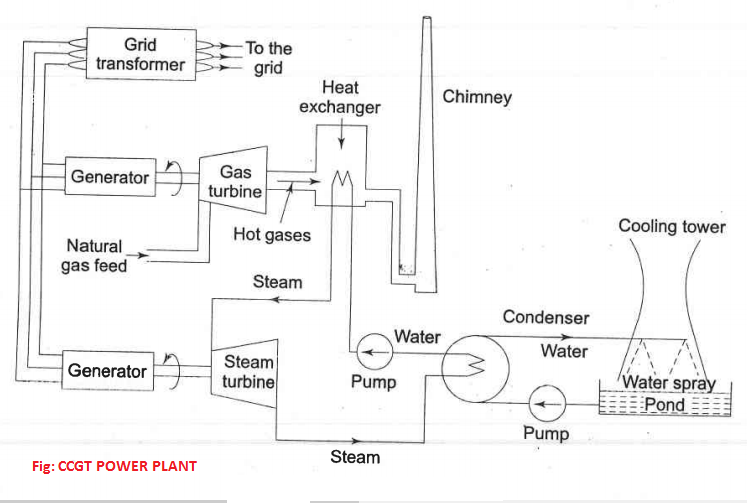
The efficiency of between 56-60% has been recorded by combining the gas power plant and conventional steam power plants.
Conclusion
Conventionally, the heat of combustion of fossil fuel is utilised for the raising of steam in boilers at high temperature and pressure. Such fossil fuel includes (coal, oil, and natural gas). The heat energy released by burning fossil fuels is converted to electricity by first converting heat energy to the mechanical form through a thermocycler and then converting mechanical energy through generators to the electrical form.
Thermocycle is a low-efficiency process. The highest efficiencies obtainable from modern large size plants is about 40%, while smaller plants may have considerably lower efficiencies. This low efficiency can be improved using cogeneration which involves the extraction of heat from the exhaust gases of these thermal plant which can be used for space heating and is particularly suitable for chemicals, paper, textiles, food, fertiliser and petroleum refining industries.
There is also improved efficiency in adopting the combined cycle gas power plant which is an improvement in both steam and gas turbine power plants. By harnessing the high-temperature exhaust gases of gas turbine power plants and channelling it to raise steam in conventional steam turbine power plants, combined efficiency of close to 60% is sure.
The earth has fixed but the abundance of non-replenishable resources of fossil fuels, with certain countries over-endowed by nature and others deficient. The world's increasing power requirements need efficient systems and diversity of generation.
As usual, you have written another one for the classrooms. Very educative and original. According to the law of conservation of energy, we cannot create energy, and any process that leverages heat must be a low-efficiency process because of the difficulty in converting heat to any other form of energy without incurring huge losses.
Thanks for sharing.
To quantify what you are saying, that is called bets limit. It is the maximum amount of energy that can be taken from given input while converting from low quality of energy to high quality of energy. Its value is 16/27 I guess.
Thanks for making it always a point to read through my post. I appreciate your time and comment. The ever increasing demand of energy needs ways of improving on the efficiency of power plants so as to reduce power cuts. CCGT and Cogeneration bring the option of improvement in efficiency of thermal plants.
Thanks for always showing up in my blog. The pleasure is mine for being able to impress you with my post. All the best.
Thanks for the kind observation. It feels good to know you value the quality post .
The low efficiency of thermal power plants is evident from second law of thermodynamics and as such it is not practical to convert heat energy to mechanical energy without temperature difference. The wider the temperature difference from the upper heat sink and the lower heat sink, the greater the energy converted and hence the resultant loss of heat to the surrounding. The obvious solution to the low efficiency of steam plants lies in the recovery of heat from flue gases before it is discharged. For gas turbine power plants, the regeneration of the hot exhaust gases is important and can be used to raise steam in conventional steam plants as you aptly described in CCGT plants. Your post is always a joy to read. Thanks for the good job.
You have a good comprehension skill and your input is very much appreciated. Thanks for the time you allocated to reading my post.
Being A SteemStem Member