Choice of Conductor Type for Overhead Line Transmission and Distribution Based on Technical Consideration
The proper choice of conductor material is very crucial if we are to ensure a good return on investment without translating so much cost to the consumers. Apart from achieving economics of power generation by adopting those generators that have the least running cost, there is need to take into consideration that the power will have to be conveyed to the consumers using conductor. If the conductivity of the conductor is poor, so much power will be lost before the generated power gets to the consumers as compared to excellent conductors.
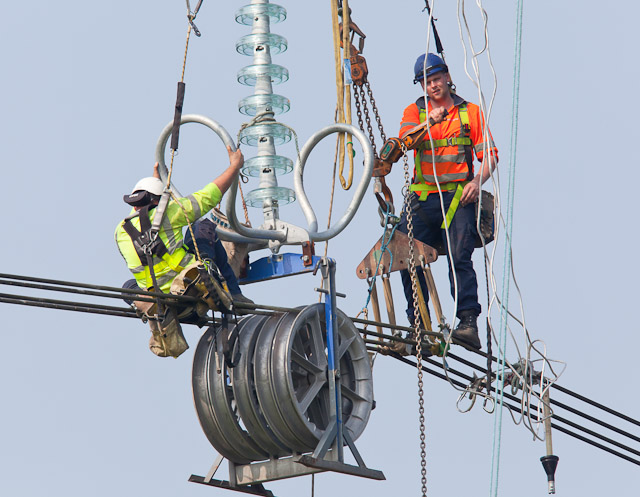
We are already in the knowing that electricity is generated mostly at a place where nature made it easy for the harnessing and conversion of the intended energy source. For example, if it is a steam plant, there is a tendency to site the plant where there are coal mines and availability of water for the condenser. The choice now becomes a compromise between the cost of transporting coal to the station and that of transmitting power to the consumers.
If it is a hydropower station under consideration, there must be water situated at a height that will impact potential energy to it. Work must be done to move the water from a lower level reservoir to higher level reservoir. Fortunately, there are natural waterfalls that are already in place. If then we need to site hydropower station there, we will not move customers from their original homes down to the area where nature has the waterfall. The logical thing to do is to generate there and find means to transport the electricity down to the consumer. The vehicle of transportation is the conductor, and if it must be a conductor, it must be a good conductor to ensure high efficiency.
Based on the above consideration, we can say that the conductor is one of the most crucial components in a power system network. There is no way we can overlook it in the transmission and distribution of electric power. The money spent on conductor material is a substantial and a significant part of the cost of the power system network. And as such, there is need to ascertain the best conductor material and the proper size that will be employed for a given project. The choice is often influenced by several characteristics of the conductor and also the application and environment in which the conductors will operate.
These attributes that are sought for includes:
- High electric conductivity (very low specific resistance)
- It should be easily available
- It should also be cheap so that it can be used for long-distance transmission and distribution without putting a strain on the finances of the utility.
- It should have a high mechanical strength (high tensile strength). This attribute is essential because the conductors of the overhead line are often subjected to both wind and ice loading. And because of weather variation, it has been experienced that during cold weather, the conductor contracts thereby shortening its length. If this contraction is coupled with wind load as a result of wind force acting on the conductor with simultaneous ice loading as a result of snow, it constitutes the worst possible condition for the conductor. Wind load act horizontally to the surface of the conductor while ice loading and the weight of the conductors acts vertically downwards. The resultant force of the conductor is the vector sum of the wind and that of the weight of the conductor plus ice.
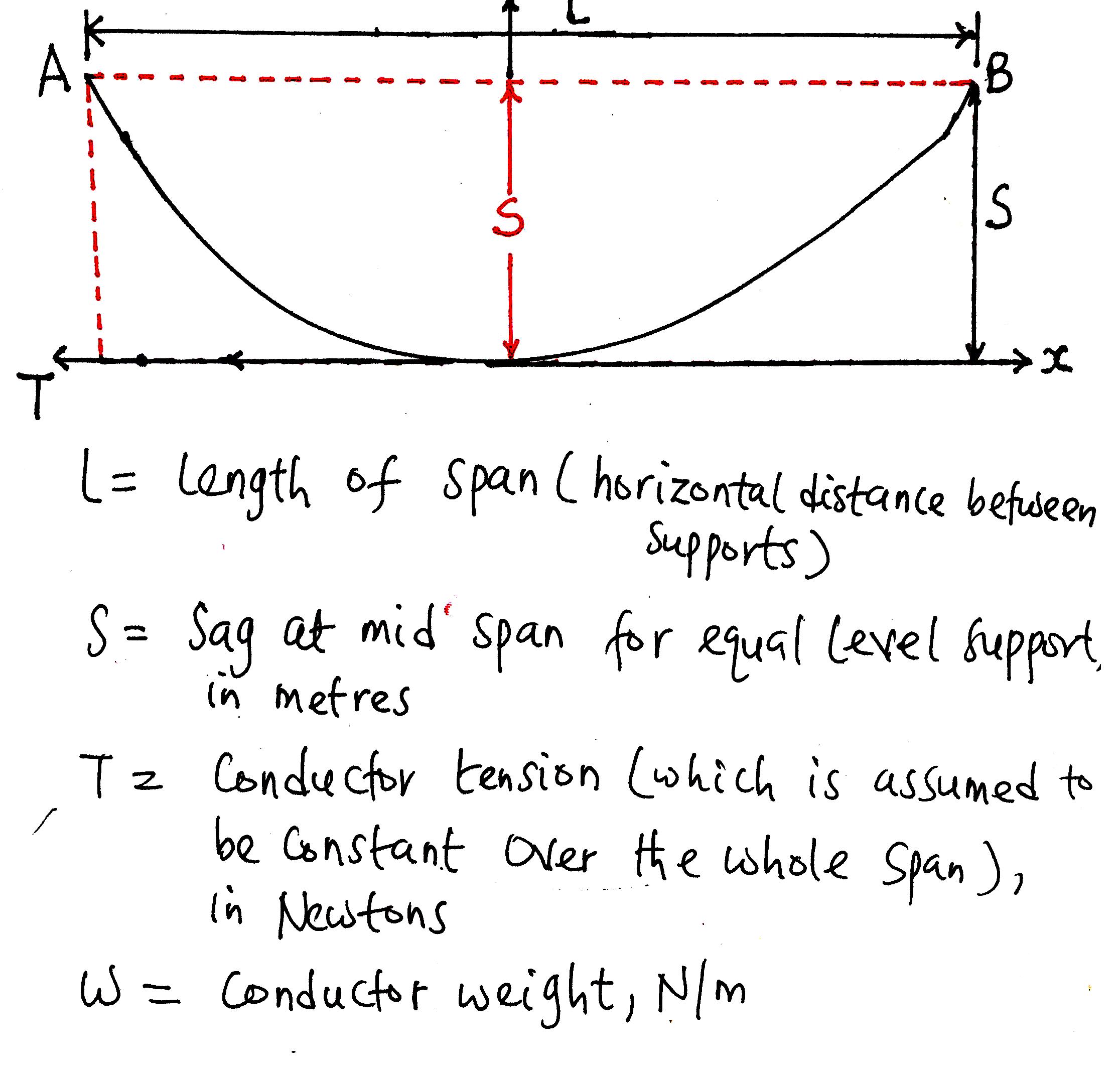
- It should not be brittle so it can be stranded and twisted to afford improved flexibility. Stranding is essential because there are cases where a solid wire cannot be applied. Solid wire is the best for conductors with a small cross-sectional area. For more substantial cross-sectional area and longer span, the use of solid conductors is not the best practice because of continuous vibrations and swinging which would result in mechanical fatigue and eventual breakage at the point of support.
- It should possess low specific gravity so that the weight per unit volume is small. This property is especially essential when you consider the fact that high specific gravity will increase the force that will be acting vertically downwards on the conductor. This force adds to the tension on the conductor and with time the cumulative effect of these forces can break down the conductor.
Considering the above analysis, we can easily see that it will be difficult for any particular conductor type to provide all the above requirements.
t = Thickness of Ice Coating
d = Diameter of Conductor
The most popular conductor material available in Nigeria is aluminium, though copper and silver are better conductors, notwithstanding aluminium is more popular because it is cheaper than the later. In general, the conductor material that is used extensively for overhead lines includes copper, aluminium, steel-cored aluminium, galvanised steel aluminium conductor steel reinforced and cadmium copper.
We will look at the different conductor types with special emphasis on cost, mechanical strength, weight to volume ratio and different applications suited for each conductor type.
Types of Conductors
There are several types of conductors currently available, some of which are more predominant than the others. They can broadly be classified as follows:
- Standard conductor
- Special conductor
Standard conductors- they include: - All-Aluminum Conductor (AAC)
- All-Aluminum Alloy Conductor (AAAC)
- Aluminum Conductor, Steel-Reinforced (ACSR)
- Aluminum Conductor, Aluminum-Alloy Reinforced (ACAR)
- Stranded Hard Drawn Copper
- Cadmium Copper
- Copper-Clad Steel
- Phosphor Bronze
All-Aluminum Conductor (AAC)
This conductor is made up of entirely hard drawn aluminum strands. It is essentially a pure aluminium (close to 99.5% minimum aluminium content). It is comparatively less expensive than other conductors but of low mechanical strength and prone to sag. Sag is the distance between the point of support and the lowest point in the conductor
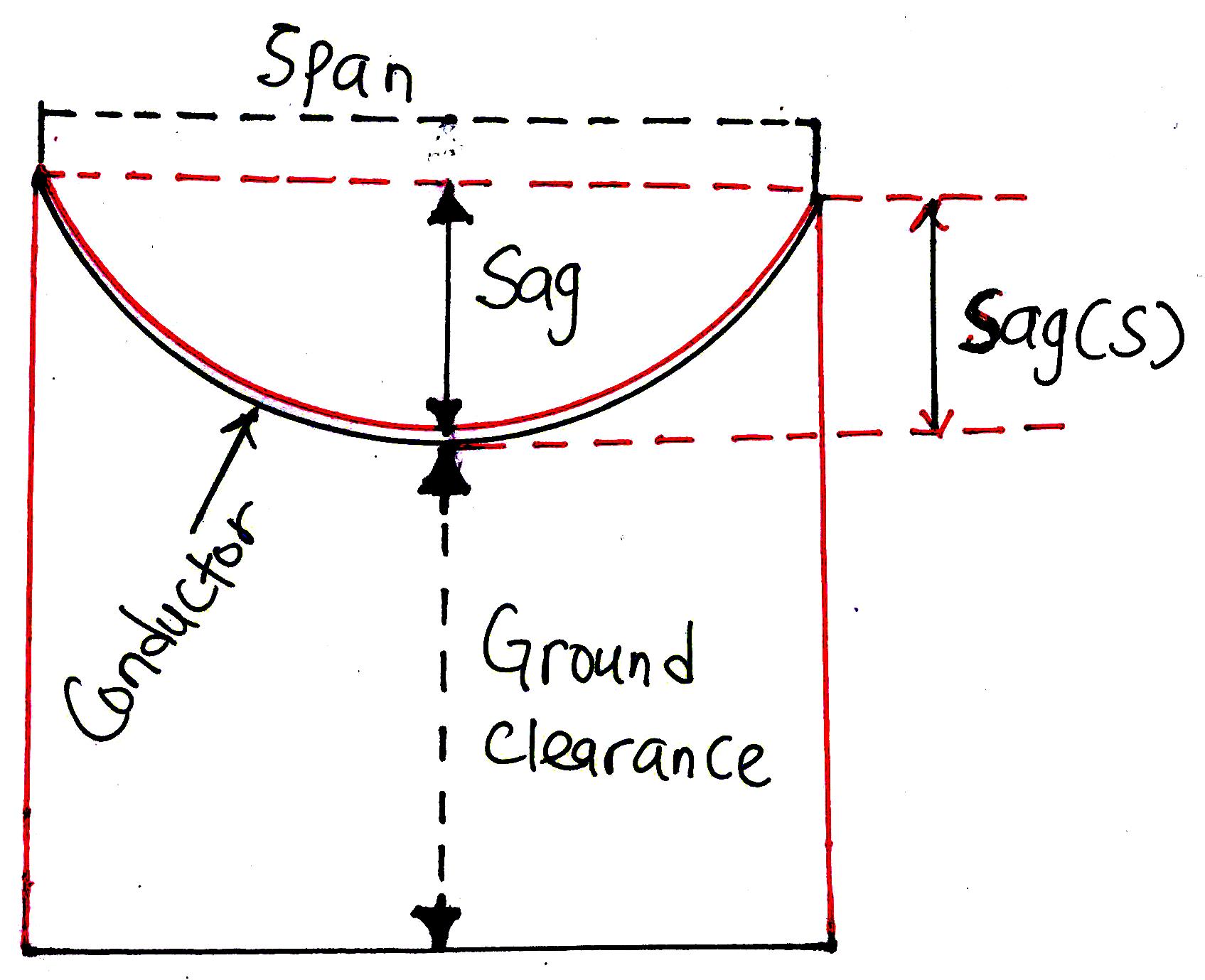
Nonetheless, it offers numerous advantages that make it ideal for installations in urban areas where space is limited and where short spans with the maximum current transfer are required.
- High conductivity
Analysis of atoms of different elements and their electronic configuration shows that In my previous posts that what makes an element a good conductor lies in it having electrons that are free to conduct. This concept of free electrons is essential for the flow of electricity. This is because the flow of electron is the flow of charge and once there is a flow of charge, there will be current electricity provided there is enough external pressure (voltage or source of electromotive force) to produce a potential gradient which will allow the electron to flow in a preferred direction.
Let us consider the electronic configuration of silver, copper and aluminum and refresh our memory as to what makes them good conductors. After establishing that they are all good conductors, we will move on and rank them in order of conductivity.
There are several types of conductors currently available, some of which are used more extensively than others. They can broadly be classified as follows:
- Standard conductor.
- And special conductors.
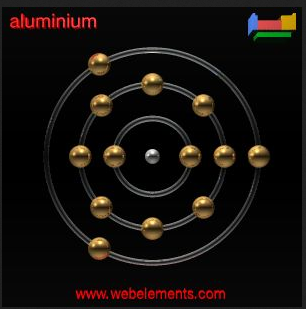.png)
Standard conductors
There are eight common types of standard conductors that have been used for so many years in the utility industry, namely:
- All-Aluminum Conductor (AAC)
- All-Aluminum Alloy Conductor (AAAC)
- Aluminum Conductor, Steel-Reinforced (ACSR)
- Aluminum Conductor, Aluminum-Alloy Reinforced (ACAR)
- Galvanised Steel
- Cadmium Copper
- Copper-Clad Steel
- Phosphor Bronze
A brief description of the characteristic features of these conductors are as follows:
All-Aluminum Conductor (AAC)
This conductor is made up entirely of hard drawn aluminium strands, and it is primarily a pure aluminium (minimum aluminium content is 99.5%). It is usually less expensive than other conductors, but it is not as strong and tends to sag more. Also, AAC offers the following properties that make them ideal for installations in congested urban areas where space is premium It is suitable for short spans where maximum current transfer are required.
- High conductivity of 61.2% IACS (International Annealed Copper Standard), or more.
- Good corrosion resistance
- And has the highest conductivity-weight ratio of all the overhead conductors.
All-Aluminum Alloy Conductor (AAAC)
This type of conductor is composed entirely of high strength aluminium alloy wires, concentric all stranded and similar in construction and appearance to AAC. Its strength is comparable with that of ACSR. It was developed to fill the need for a conductor with higher strength than that available with AAC but without steel core.
The equivalent diameter of this conductor is typically used to replace ACSR conductors. The AAC conductor offers the following properties:
- Have comparable thermal rating.
- Improved strength-to-weight ratio.
- Lower electrical losses.
- And superior corrosion resistance.
These factors make AAAC conductor an attractive choice for installation on the seacoast and other areas where corrosion problem prevails.
Aluminum Conductor, Steel-Reinforced (ACSR)
This is the most common type of conductor used today. It is a stranded conductor arranged in a concentric form and is made up of of one or more layers of hard-drawn aluminum core stranded with a high strength galvanized steel core. The core may be single wire or stranded depending on size.
The high tensile strength combined with excellent conductivity give ACSR several advantages:
- Because of the steel core lines designed with ACSR elongate less than other standard conductors, yielding less sag at a given tension. Therefore, the maximum allowable conductors temperature can be increased to allow a higher thermal rating when replacing other standard conductors with ACSR
- The high tensile strength of ACSR makes it immune to breakage, and we can install it in areas that are prone to wind loading.
- ACSR is less likely to be broken by falling tree limbs.
Aluminum Conductor Aluminum-Alloy Reinforced (ACAR)
This type of conductor consists of aluminium strands reinforced by a core or distributed wire of higher strength to achieve an excellent balance between mechanical and electrical properties. ACAR offers the following properties:
• High strength-to-weight ratio.
• Excellent corrosion resistance, and
• Utilize simple termination hardware.
Galvanised Steel
Galvanised steel is employed in rural areas for voltage range up to 11KV. It is used when the target is to reduce cost as it is cheap, but it has the disadvantage of having low conductivity, high internal reactance and prone to eddy current and hysteresis loss. These disadvantages limit its use to telecommunication lines, guard wires, stay wires and earth wires.
Cadmium Copper
Cadmium copper conductor is a copper conductor alloyed with 1 or 2% cadmium. The introduction of cadmium decreases the conductivity of copper by about 17%, but this is counterbalanced by the increase in tensile strength of copper to about 40%. This additional increase in tensile strength is advantageous as it will enable the economical use of cadmium copper for longer spans with a smaller cross-sectional area of the conductor.
Copper Clad Steel
Copper clad steel is formed by welding a copper coating on a core of steel wire. The introduction of steel wire core increases the tensile strength of copper considerably as compared to all copper conductor. This improvement in tensile strength makes it the ideal conductor for application where long span cannot be avoided as in river-crossings.
Phosphor-Bronze
When the atmosphere is saturated with harmful gases such as ammonia or when the span is exceptionally long, phosphor bronze comes in handy as an overhead conductor. It is formed by introduction of some strands of phosphor bronze to the cadmium copper.
Conclusion
The conductor is a major component of the power system network. The money invested in conductor material is quite significant, and effort should be channelled towards the right choice of conductor, and this must be based on economic consideration, application, environmental conditions and other numerous technical considerations. When you look up as you walk along the street, you will notice overhead transmission and distribution lines, and you will marvel why aluminium or aluminium alloyed conductors predominates with regards to the material used for the construction of these lines since they are not better than copper and silver in conductivity. The reason they are so attractive is majorly due to their widespread availability and cheapness as compared to their counterparts.
The design of electric power line is normally done keeping in mind the electrical, mechanical and thermal requirements. The electrical design involves selection of voltages, selection of conductors, voltage control; and selection of protective gear.
The mechanical design requires stress and sag analysis and the design of supports and cross-arms. The support and the conductor must be strong enough to withstand simultaneous ice and wind loads acting on it.
Two of the most important mechanical properties of a conductor is the rated breaking strength and the stress-strain relationship. Both of these properties of the individual strands of which the conductor is composed coupled with the design used to incorporate the conductor. The electrical characteristics of a conductor are one of the most important considerations when selecting a conductor.
The major electrical attributes that need to be considered in the design of a transmission line are DC and AC resistance, inductance and inductive reactance, capacitance and capacitive reactance. The conductor resistance determines the conductor losses and limits the maximum allowable current carrying capacity of the conductor.
References
Being A SteemStem Member
There is no single conductor that is capable of delivering on account of electrical, mechanical and thermal attributes. A compromise has to be made in terms of the best possible attribute desirable for a particular application and prevailing condition. Another way is to synthesis the ideal conductor by alloying to overcome the major defects and be able to to perform with high efficiency. Very good post, as always. Thanks for sharing and hope to see another work from you soonest.
Thanks for making out time to read the post. I appreciate your input.