Experiences And Pictures From A Just Concluded Memorable Six-Month Internship Programme Including It's Defense
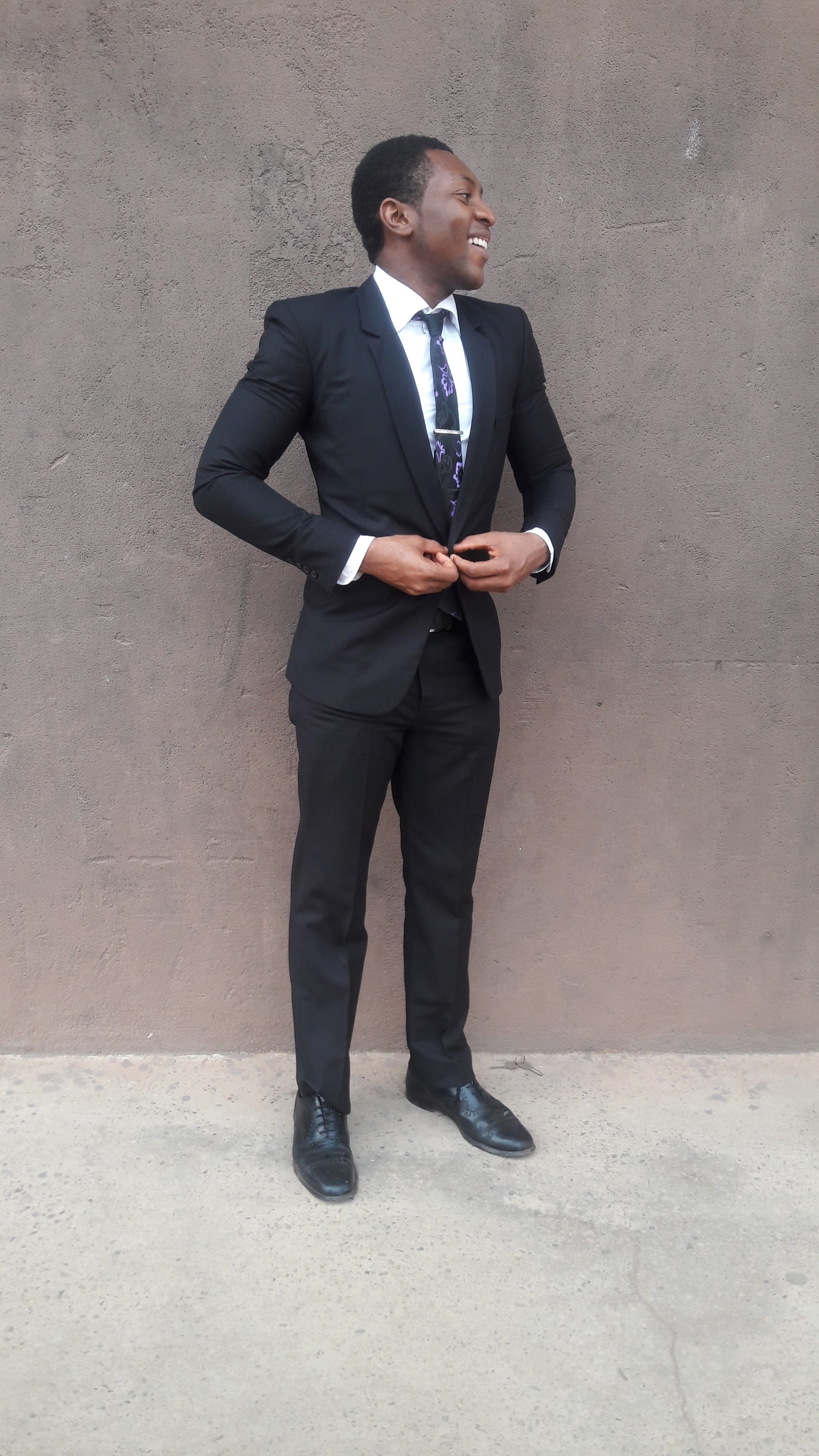
Hey guys, thought I'd share some amazing experiences and pictures from my recently concluded I.T program which I did at an awesome engineering company; CONTOUR GLOBAL SOLUTIONS NIGERIA. The truth is I would've shared this much sooner but I've been really tied down with some crazy workload in school. Being currently and constantly hit with tasks from my ongoing project work, tons of brain racking engineering courses and other time consuming extra-curricular activities is no joke. I barely have time for anything else which unfortunately also includes steemit (which is quite painful by the way).
I guess it isn't easy to slave for two masters after all since I Gotta leave school on a high(with a CGPA on steroids) lol. Well, enough of all that, in this post I'll be giving a summary of my experience(s) during the total duration of six-months which I spent working at CONTOUR GLOBAL. So, without further ado let's get right into it.
A Brief Summary Of My Received Training And Experience At Contour Global
Well, the company where I did my six-month internship; Contour Global Solutions Nigeria was and is still contracted to Nigerian Bottling Company(NBC) which is the bottling company for The Coca-Cola Company in Nigeria. So this branch of the company is located within the NBC company premises. We were charged with the job of producing Electric power, steam, CO2 for the main Coca-Cola bottling plant 24/7 including helping to cool it's entire office complex and structures with the aid of three industrial sized chillers. This means that the company is basically divided into four sections;
- The power production section
- CO2 production section
- Steam production section
- Chiller section.
Power Generation At Contour Global
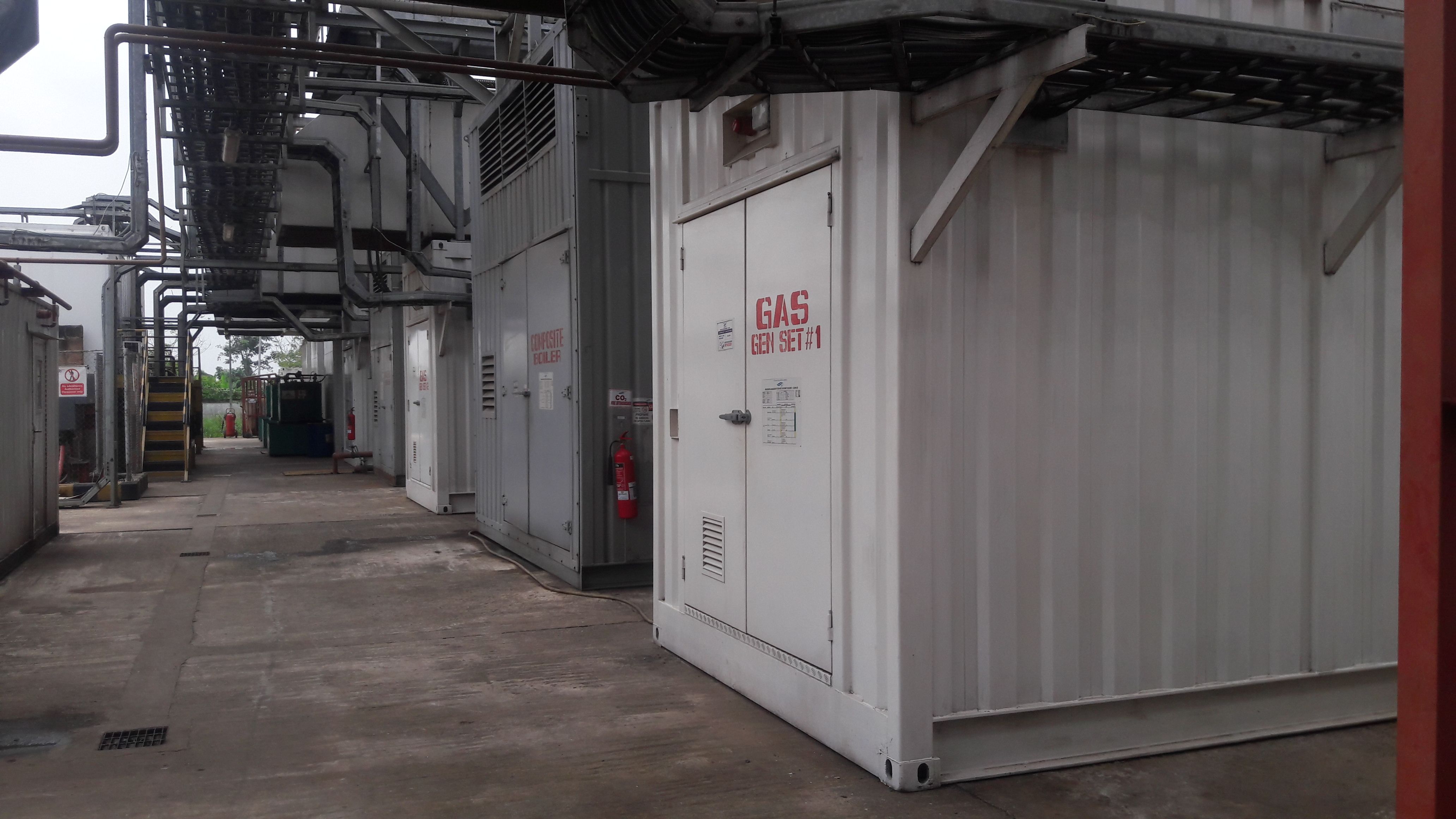
We helped provide power with the aid of three gas generators and three diesel generators, with the gas generators being rated 1.160MW each and the diesel generators also being rated slightly lower than it's gas counterparts with a rating of 1.100MW. As an intern on site, I helped the machine operators and other site engineers ensure that the generators were always working on maximum optimal conditions as there was practically no margin for error.
A split second blackout leads to the unforgivable loss and wastage of material resources, since production was always ongoing 24/7 on site except during times of scheduled routine plant maintenance operations when production was at a low or even at zero. And thus, since a blackout could potentially lead to our company being slapped right in the face with a million dollar bill for incurred production losses, it was therefore imperative that power supply be maintained at a constant and steady level at all times.
It is surely one thing to promise to do something and it is an entirely different thing to actually fulfill that promise no matter the circumstances; favorable and unfavorable. Believe me, keeping the generators running at all times is no joke as we always had to perform maintenance and repair jobs frequently just to ensure that the engines run smoothly and seamlessly without issues and the days when we're free from maintenance jobs we all had to keep an eye on the SCADA(Supervisory Control And Data Acquisition) computers in the control room to ensure that the engines are running smoothly.
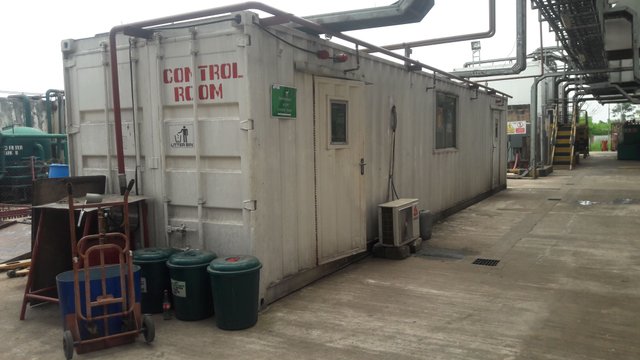
The three gas generators where basically the main generators while the diesel generators where mostly used as backup generators during maintenance of any of the gas generators, depending on the load requirement at that particular time, since the whole system was designed to make more and more generators come up automatically(one by one starting from the gas engines) and synchronize together to handle the current load as the total load requirement increased significantly. All of this was done simply to maximize profit and reduce cost since natural gas is basically cheaper than diesel(or at least in this part of the world).
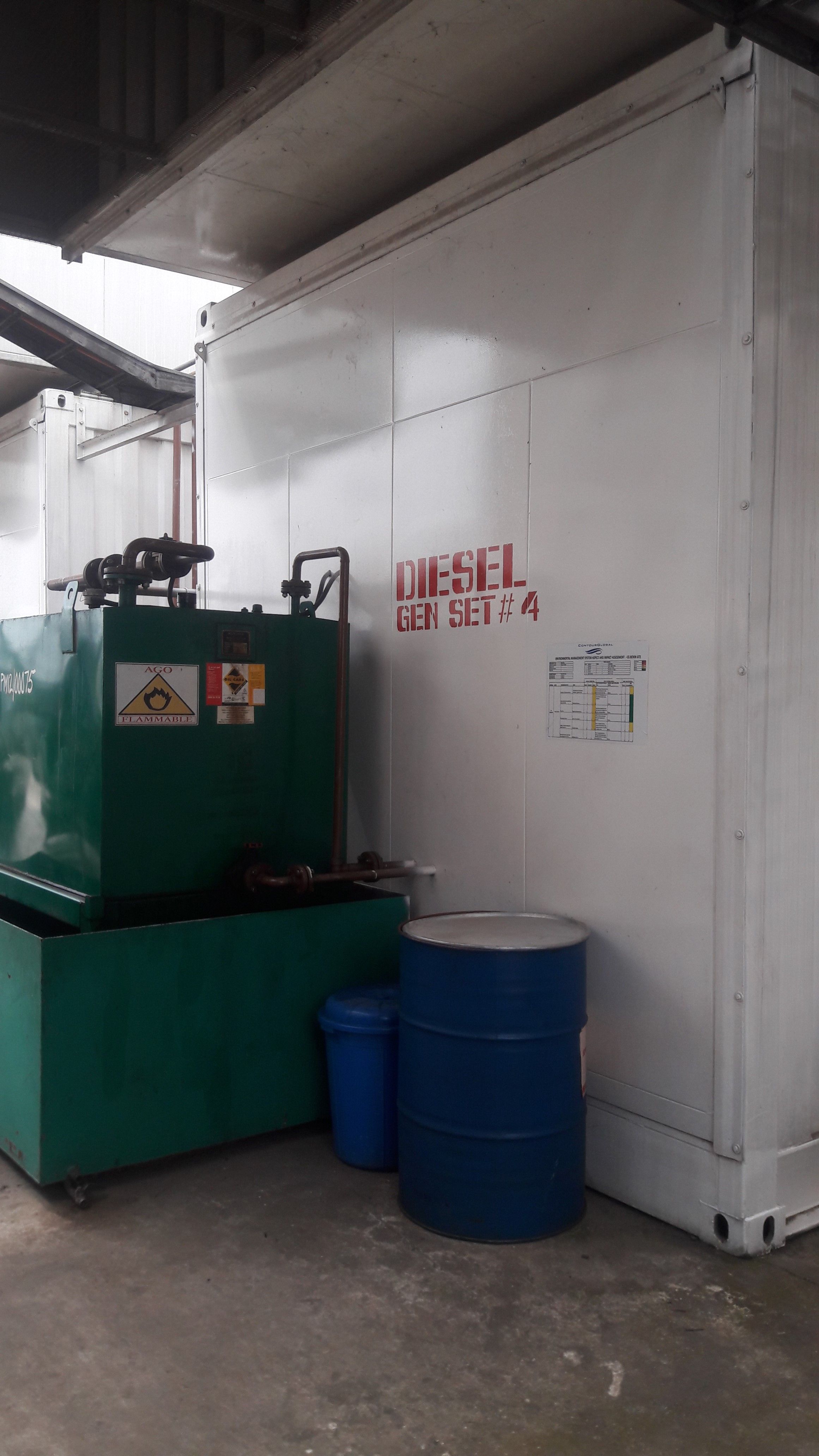
I remember one particular time when we were relaxing in the control room and then from the HMI(Human Machine Interface) and SCADA computers we discovered that the oil temperature of one of the running gas generators was abnormally on the high side. We decided to observe the situation closely for a couple more hours before deciding on what to do. Long story short, the engineers decided we had to remove the oil coolers and clean them thoroughly as they were probably dirty and would be the cause of the high oil temperatures(Oil coolers are basically engineered to efficiently reduce oil and fuel temperatures in an engine).
I thought it was going to be an easy job but didn't realize until days into the yet to be completed job, that it was going to be a tough one. We spent a total of three days on the job as for some reason unknown to me, the designers of the generator decided it was best to place the oil coolers in a really tight and hidden compartment down below. We had to loosen more than half of the generator components and compartments simply to get to the oil coolers which were four(4) in number. I think I even lost some weight after that very job lol. It was that tedious. Below is a picture of me cleaning one of the oil coolers with a steam washing machine;
On another occasion we did a 30,000 running hour maintenance job on one of the gas generators. Again long story short we spent a month on that very job. Yep, I'm not crazy and I know exactly what I'm saying. We spent a total of 4weeks on that job, and for good reason too. As we did a major overhaul of the entire generator. Meaning we changed or replaced basically everything in the generator(except for the body frame lol). From the bearings, cylinders, connecting rods, pistons, crank and camshaft, oil coolers, turbocharger, air charge cooler, coil on plugs to the cylinder heads, all of it had to be removed and each part replaced and fixed in their perfect positions. This means I spent a whole month of my total 6months there on a single job. Yeah. I know it sounds crazy but it's true. Okay, so now let's talk a little about the CO2 plant.
The CO2 Production Plant
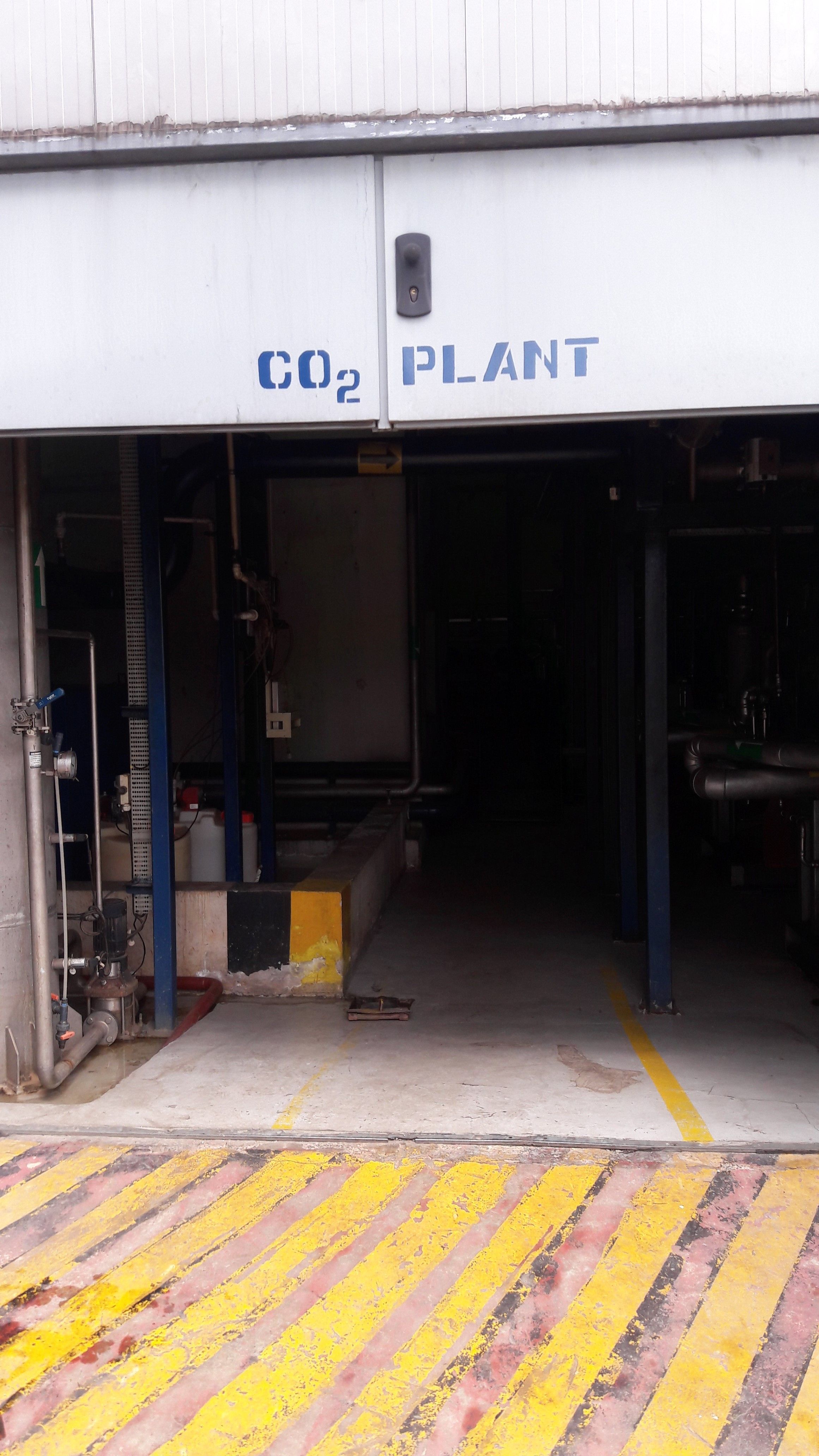
Remember that hissing sound you hear whenever you open a Coca-Cola bottle or even still most fizzy drinks? Well, apart from it being a result of the equalizing of the pressure differentials within and outside the bottle, it occurs due to the release of Carbon(IV)Oxide or CO2 for short, as CO2 is essential to preserve or aerate these fizzy drinks for the long term and this is where we come in again. Contour Global has a CO2 plant which provides NBC with the CO2 needed to produce their drinks.
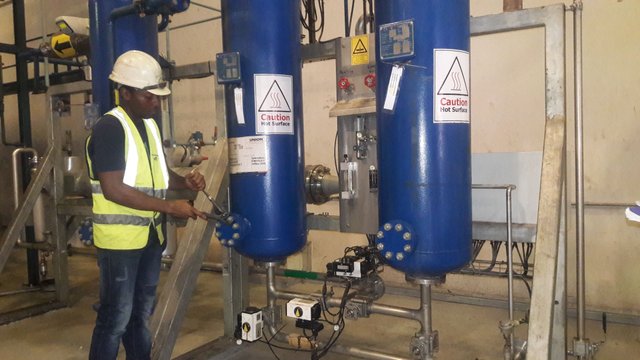
The CO2 is produced by simply engaging a hydrocarbon in a combustion reaction. This leads to the release of CO2 and several other flue gases, from which the flue gases can be captured from a series of chemical processes. In Contour Global the hydrocarbon used is Natural Gas and the CO2 is captured with the aid of a Monoethanolamine(MEA) solution which has great CO2 absorption capabilities, don't worry I'll spare you all the lengthy complex details of all the numerous processes involved, but the captured CO2 after undergoing several refining and purification processes to make it food grade CO2 is then finally stored in two very large vertical CO2 storage tanks with each tank having a storage tank of 50tonnes(the two white vertical tanks in the second picture of this post). Below is a picture of me taking some readings from one of the two CO2 compressors.
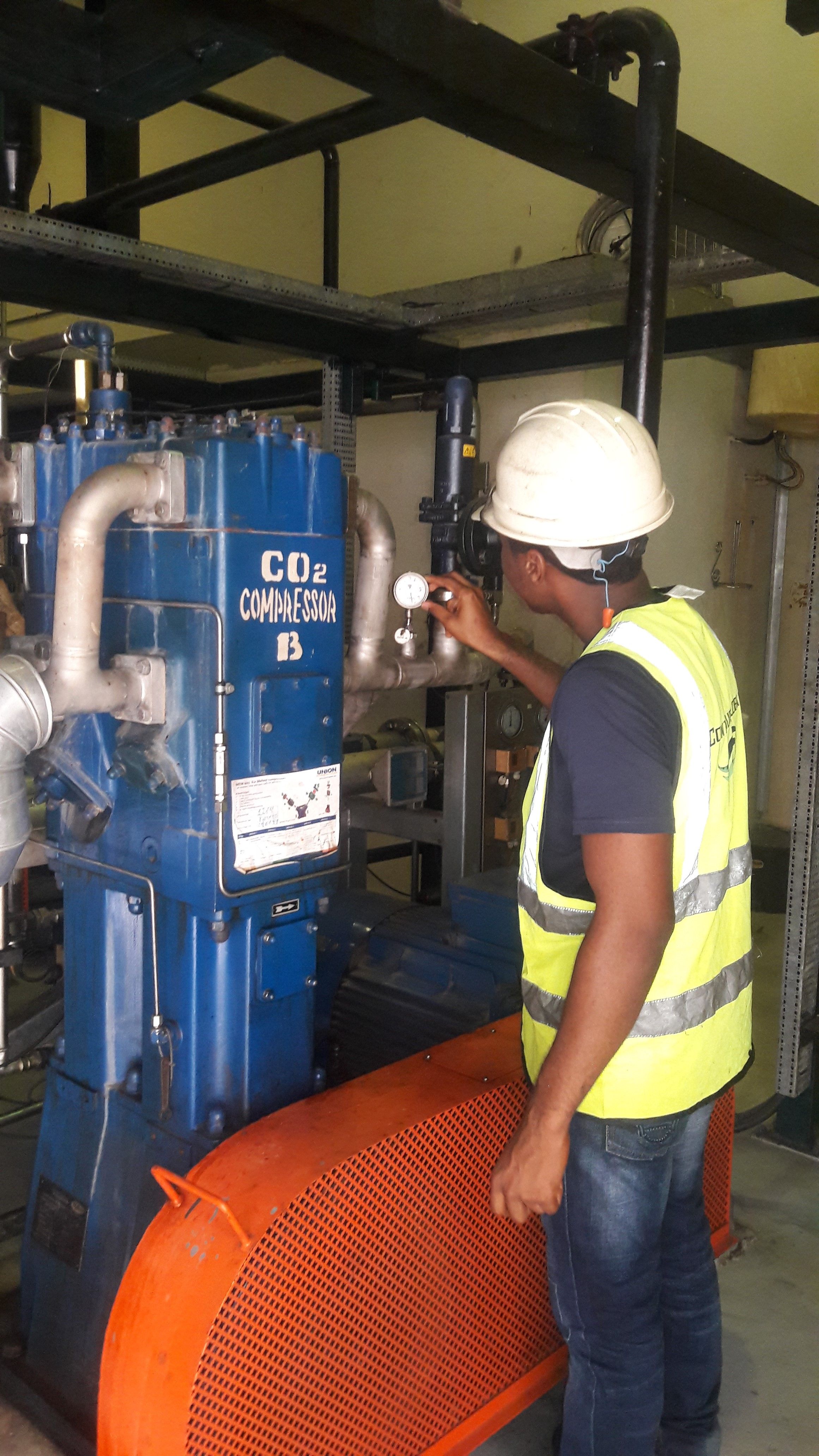
Most of the processes in the CO2 plant were fully automated and so we really didn't have to do much work there as such. Apart from refilling the MEA tank with new MEA from new MEA drums and also performing routine manual cleaning of the machines like the CO2 compressors, dehydrators and the likes. Below are some pictures we took with Mr Robert(A UNION Engineering CO2 expert, consultant and engineer).
Steam Production At Contour Global
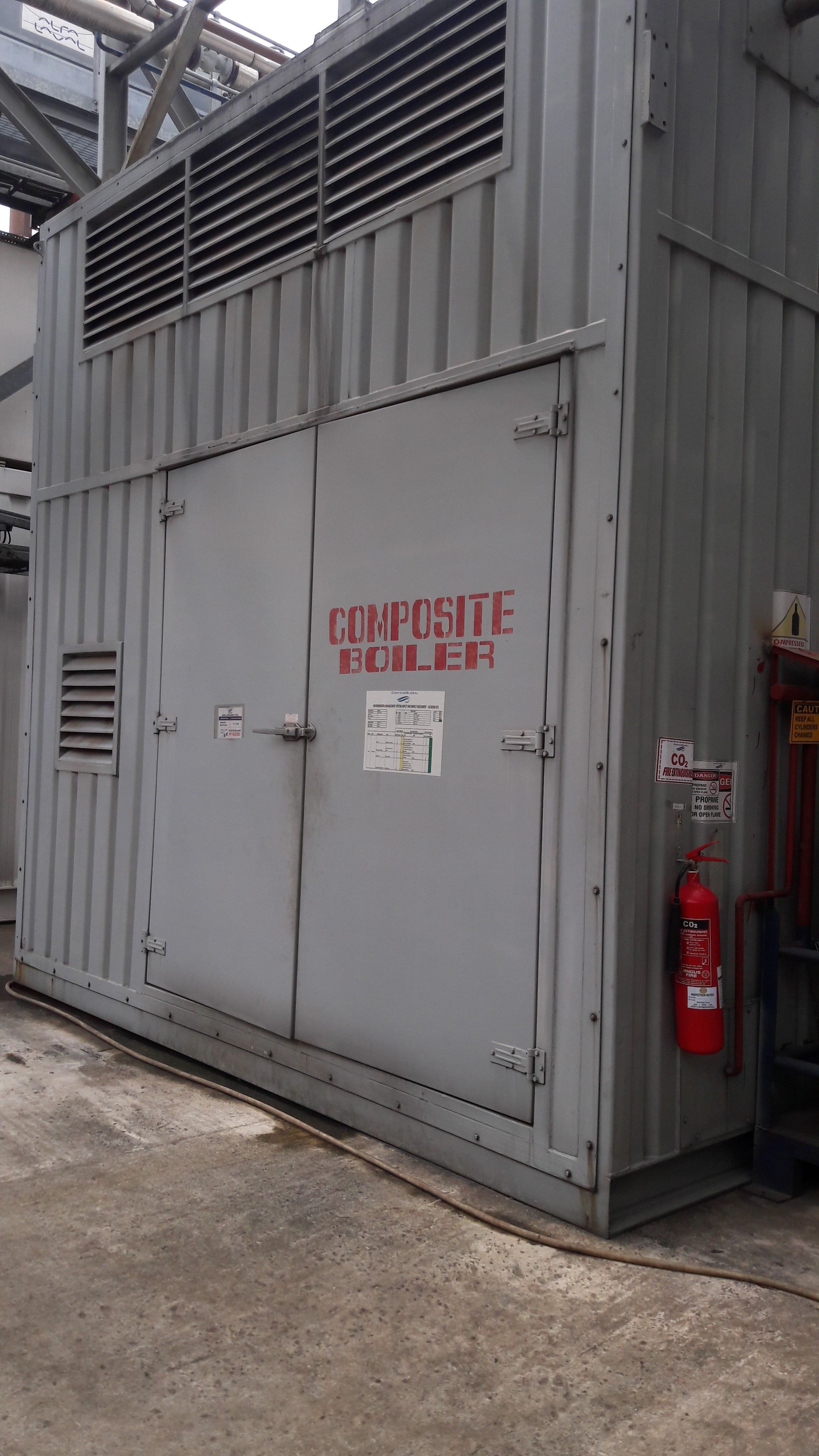
With the aid of two industrial sized boilers we also produced saturated or superheated steam for the main NBC production plant depending on their demand specifications. The steam produced is used by NBC to help wash their used bottles to ensure they're super clean before filling them up again with the liquid they contain. That way you wouldn't have to worry about spotting cockroach wings in your drinks when you open them up.
Think of a boiler as the kettle in your home, only with insane proportions, meaning the boiler is like one giant kettle which heats up an obviously large volume of water or other fluids within it's pressurized enclosure to generate steam. The first boiler at Contour Global being a composite boiler uses natural gas as it's source of fuel for heating up the water to generate the needed steam while the second boiler is a waste heat boiler which uses the waste heat or exhaust gases from the generators running at that very time as it's source of fuel. This thus tremendously reduces environmental pollution to the barest minimum while also increasing the entire efficiency of the whole system due to this clean energy recycling process which reduces heat losses.
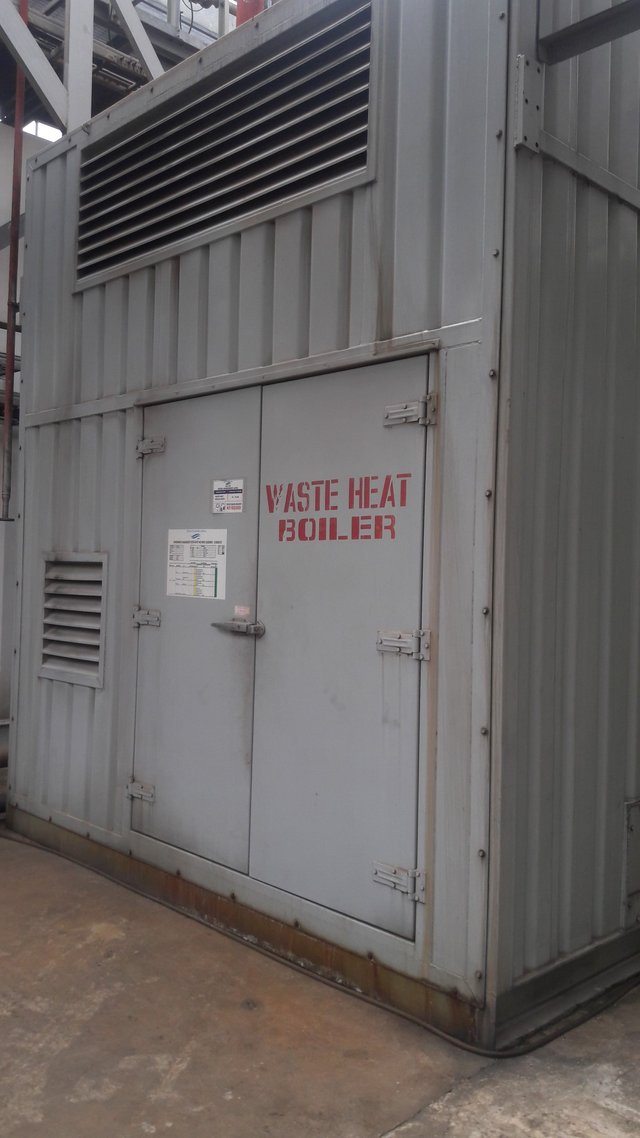
Again both boilers were fully automated and as such there was almost always little or no work to be done here. So, now let's talk about the last part I'm still yet to talk about.
The Industrial Chillers
A chiller is basically a refrigeration system which cools a fluid or helps dehumidify air either by means of a vapour-compression or absorption-refrigeration cycle. The company had three industrial chillers which served different important purposes; one of which includes the fact that it was used to provide adequately air conditioned low cooling temperatures for several offices and buildings within the company's premises. They were also used for lowering the temperatures of the drinks and bottles in preparation for the addition of CO2, since the CO2 cannot just be added while the drinks are at room temperature but rather the temperatures of the drinks must be lowered first before CO2 can be administered.
I spent quite a great deal of time operating the chillers. This was because, hourly readings of several parameters had to be taken continuously and consistently every single time, so as to ensure that the chillers are cooling properly because any fault with the chillers leads to a pause in general production. So the chiller was as highly important as the generators generating power. Below are some pictures taken during an overhaul of one of the chiller's reciprocating compressors.
Apart from regularly cleaning the chiller housing, cleaning the chiller machines and parts such as the condensers and compressors, I also had to take hourly readings of values of parameters such as the;
a. Suction pressure
b. Tank cold well
c. Cumulative running hours
d. Oil pressure
e. Discharge pressure
f. Alarm setting
g. Oil setting
h. Oil return temperature
i. Discharge Temperature
The value of the cumulative running hours of each chiller is very important as it gives the total hours for which the chiller has been in operation, this helps for pre-scheduling of maintenance operations on each chiller. For example after every 1000 running hours the chiller is serviced. Other maintenance can be done after 3000, 5000 or even 10,000 running hours. So although other values are important, the cumulative running hours is the most important and as such all these values must be recorded each and every hour of the day. Could be pretty tiring and boring to do this at times I must confess. But someone has gotta do the job which is where I come in. Of course, who better to give such job to than the I.t guy lol. Below is a picture of me taking the hourly readings of one of the chillers.
Well, that's it for the main sections of the company, and I must say that it was a really fun experience and apart from the yelling instructors, the times when I was extremely fatigued and almost succumbed to sickness due to the intense nature of the jobs at times, it was really fun. I enjoyed my entire experience there and I'd do it all over again if presented with the opportunity. And oh, I apologize for the nature of the pictures I took when talking about the machines. The company is pretty strict when it comes to the issue of taking pictures of the company's machines. Meaning which, when, how and what kind of pictures can be taken there are strictly scrutinized. So these are the ones I could kinda manage. Nonetheless, I hope you liked them though!
The Perks Of Working Alongside A Bottling Company
I need not say much, just see for yourself.
My I.T Defense In School After Full Resumption
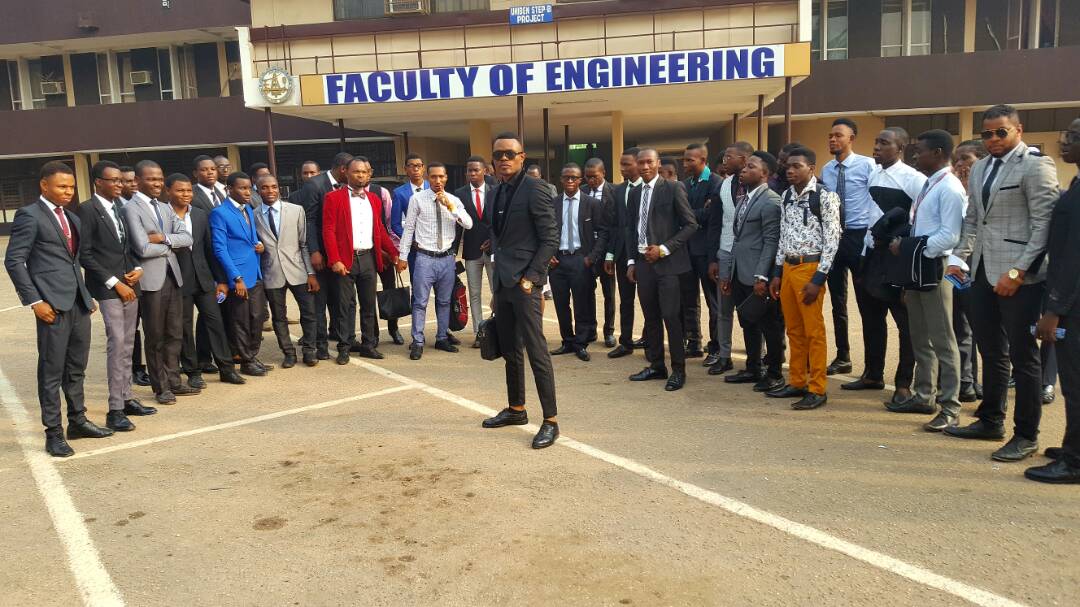
When I resumed school we were told our I.T defense was set for the next friday. And we were then shared into groups of fours prior to the day of the defense, and as usual we were given our do's and don'ts on the D-day. Most of us were nervous at first but then we realized there was nothing to be scared for since we actually knew what we did and as such could defend all our activities. Still easier said than done though lol!
Anyways I couldn't take pictures of myself standing before the panel of probably angry judges as lecturers in my department(Mechanical Engineering) hardly smile at all. Most of them even have cracked faces lol! Anyways we were simply asked individually to summarise our working experience at each of the companies we worked. Meaning all what you learned, your challenges there, limitations encountered, practical relevance of the job and so on, and oh, all within a space of 10 to 15 minutes, after which you will be fired with questions from the lecturers from every single angle. You could really cut the tension in the hall with a knife lol. Anyways, below are some of the pictures I took before and after the I.T defense.
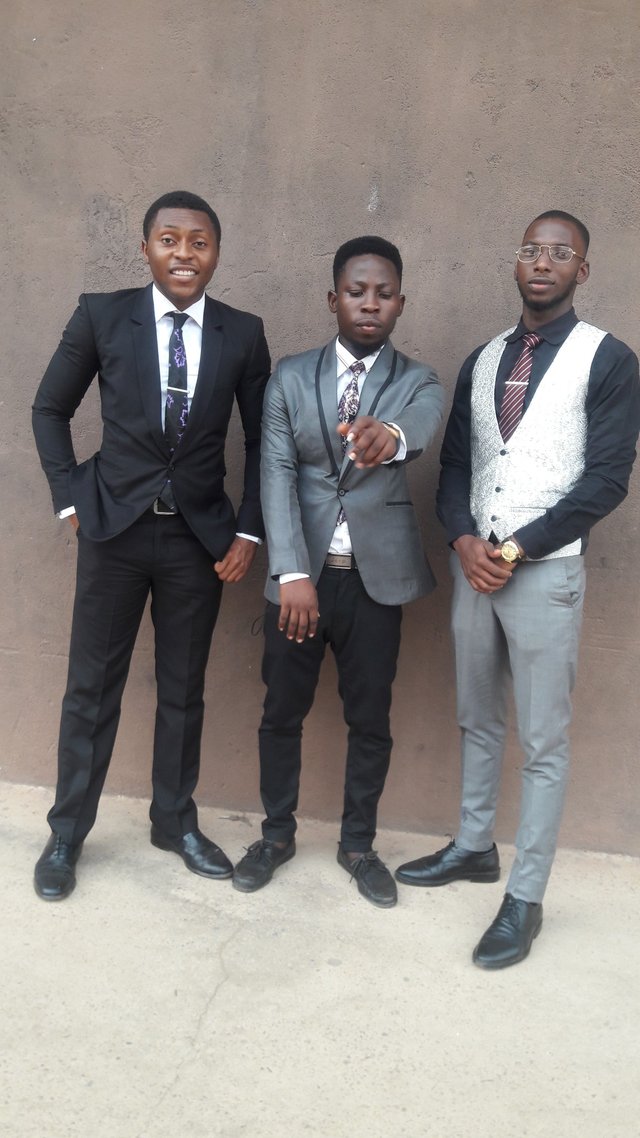
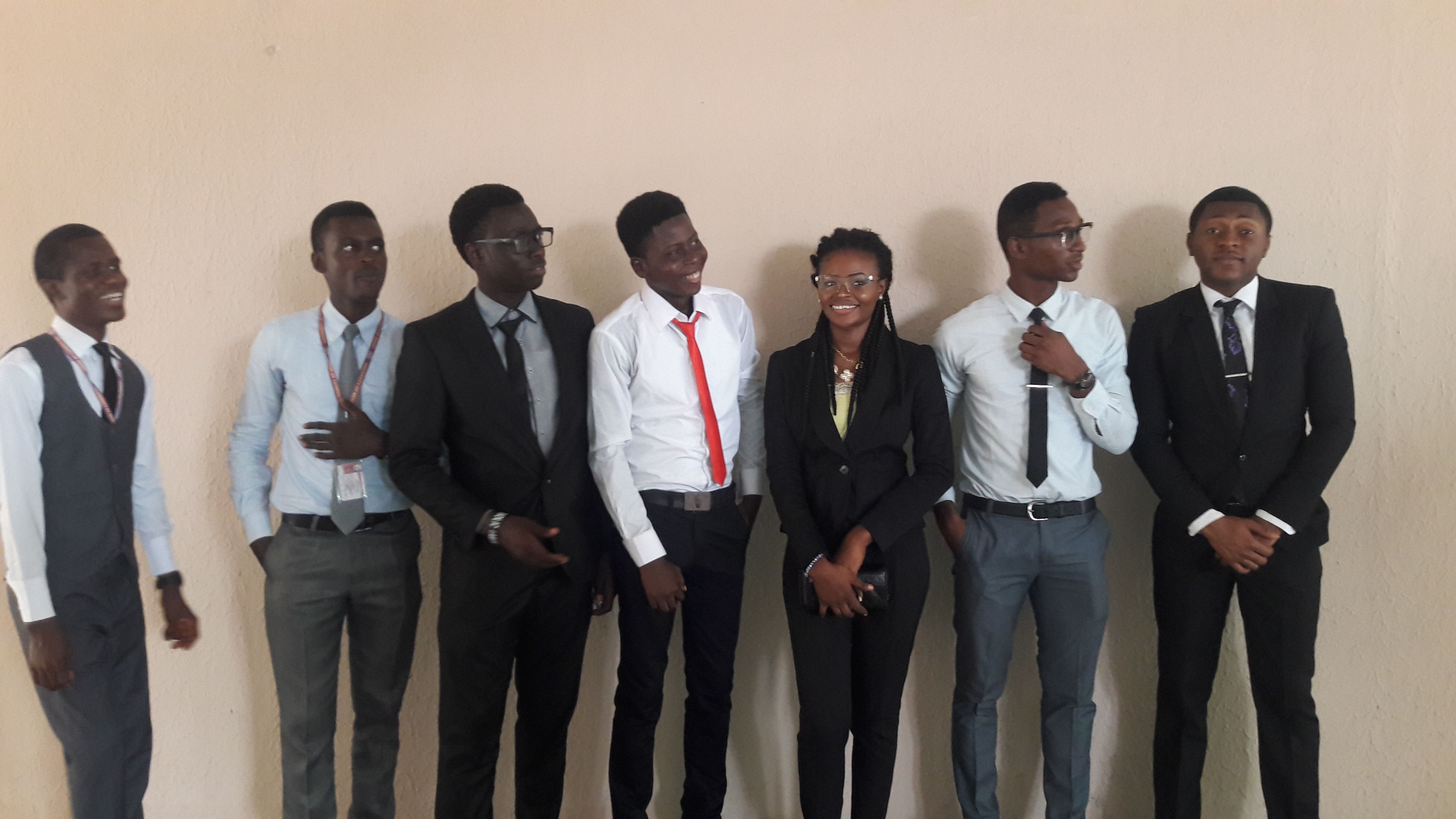
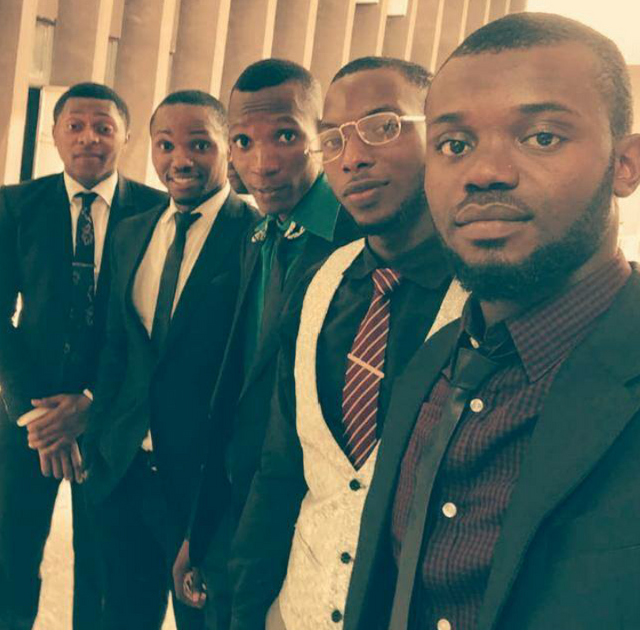
That's all folks, hope you enjoyed the jolly ride. Have a great day/night! :)
IMAGE CREDIT: All images and pictures were taken with my Samsung GalaxyJ7 phone.
To enjoy more interesting Science, technology, engineering and mathematics related posts, follow the @steemstem account, check out other wonderful posts using the #steemstem tag and also be sure to rub minds with other like minded individuals on the steemstem chatroom at steemit.chat and on discord.
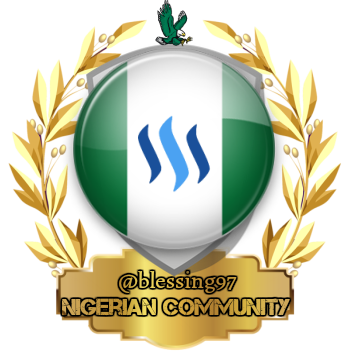
Many thanks to @gbenga and @jodipamungkas for this lovely badge.
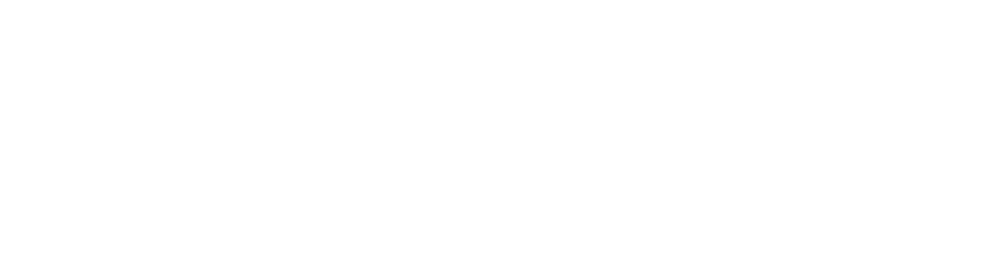

This is a test comment, notify @kryzsec on discord if there are any errors please.
Being A SteemStem Member
That's one of the beauty of Internship
A very good one
Done so well for yourself
Wish you the best brother
Thanks alot. Glad you came around.
Wishing you success in your just concluded I.T defense I also pray for God to grant you your heart desire of graduating with a high CGPA
Amen, amen and amen!!! Thank you very much!
Your expressivity of point(s) is fascinating, and complements your photography, what else can i say, with such detailed piece about your Industrial training, i can confidently say without missing words that your GCPA is smoking weed.
Wishing you all the best bro as you wrap it up this year...you can walk by my site anytime