Era de la Automatización en plantas industriales
El ser humano siempre ha sentido fascinación por el futuro, personas de la historia como el escritor, pintor, cientifico, etc. Leonardo da Vinci (15 de abril de 14522 a 2 de mayo de 1519). Actualmente, podemos notar que la era de la automatización se está instalando en todos los servicios que recibimos, con la promesa de mejor eficiencia y ahorro de tiempo utilizando cada vez más con máquinas que con personas. Sin embargo las maquinas son monitoriadas frecuentemente por profesionales para garantizar un buen funcionamiento.
En la industria la calidad de los productos es la primera prioridad para satisfacer los servicios y necesidades de los consumidores. La instrumentación es la forma más práctica para mantener dicha calidad haciendo las mediciones mas optimas con una alta exactitud y precisión.
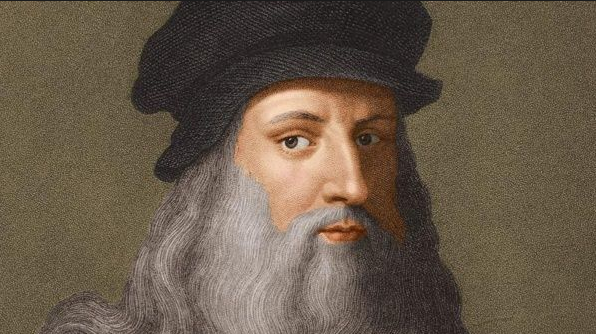
Es imaginable las industrias o plantas modernas sin utilizar sistemas de instrumentación y control. Todos los procesos industriales como: Alimenticios, Siderúrgica, Industria papelera, Petrolera, etc. Es absolutamente necesario controlar variables fundamentales como: presión, volumen, temperatura, etc. para evitar que los productos salgan fuera de especificación (Producto no deseado) y problemas operacionales (Perturbaciones).
Por ejemplo, la instrumentación en una planta de procesamiento de gas natural generalmente se compone de un sistema de dispositivos neumáticos, hidráulicos y electrónicos para medir y controlar todas las variables del proceso que son fundamentales para el funcionamiento de la planta. Así mismo, las computadoras se incluyen en el sistema de instrumentación para manejar funciones tales como la recopilación y transmisión de datos, almacenamiento masivo de datos, visualización, alarmas, registro y control. Desde la electrónica de circuitos integrados, específicamente el microprocesador, muchos tipos de instrumentos son cada vez más inteligentes y eficientes.
Selección de instrumentos:
Frecuentemente, la selección del tipo de un instrumento está predeterminada por la disponibilidad, compatibilidad con el resto del sistema y costo. Sin embargo, hay casos en que la elección de instalar instrumentación neumática o electrónica debe hacerse comparando las características de cada tipo. La tabla 1 y tabla 2 presentan las características de los instrumentos neumáticos y eléctricos.
Intrínsecamente seguro, sin circuitos eléctricos. | Mayor precisión. |
Compatible con válvulas. | Compatible con computadoras. |
Fiable durante un corte de energía por un corto período de tiempo, dependiendo del tamaño del recipiente de sobre voltaje. | Tiempo de tránsito rápido de la señal. |
Sujeto a contaminantes del sistema de aire. | Contactos sujetos a la corrosión. |
Sujeto a fugas de aire. | Debe ser purgado con aire, a prueba de explosiones o intrínsecamente seguro para usarse en áreas peligrosas. |
Las piezas mecánicas pueden fallar debido a la suciedad, arena, agua, etc. | Sujeto a interferencia eléctrica. |
Sujeto a congelación con presencia de humedad. | Más difícil de proporcionar para una operación positiva a prueba de fallas. |
La velocidad de control está limitada a la velocidad del sonido. | Requiere la consideración de los detalles de instalación para minimizar los puntos anteriores. |
Identificación de instrumentos:
Un instrumento puede ser de función especifica, como un indicador de temperatura (TI), o una combinación de funciones, como un controlador-registrador de flujo (FRC).
La Figura 1. presenta los símbolos comunes en las hojas de flujo de procesos, también llamado Diagramas de tubería y instrumentación. Existen designaciones de letras aceptadas de la Sociedad de Instrumentos de América (Figura 2) y sus significados cuando se usan en identificaciones de instrumentos. Se pueden encontrar requisitos de identificación especiales en ciertas aplicaciones.
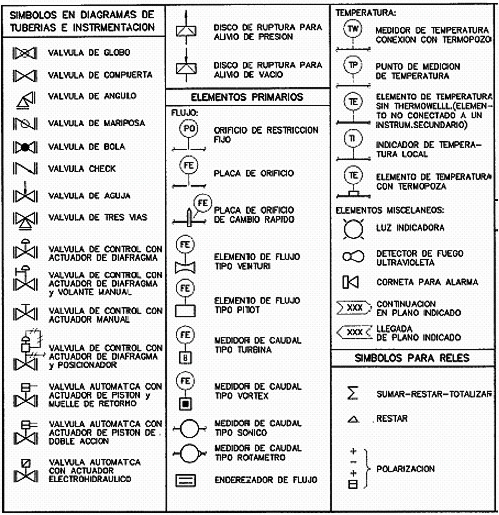
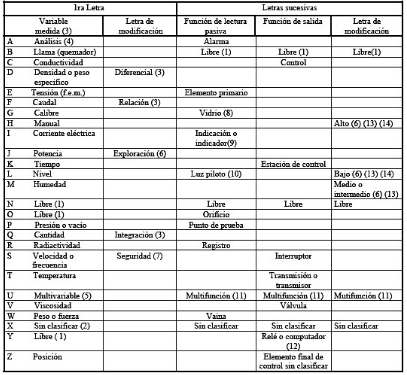
La fuente de alimentación neumática es conocida como el sistema de aire de instrumentos. Las principales consideraciones de un sistema de aire de instrumento son:
Capacidad adecuada: La capacidad mínima del sistema debe ser la suma de los requisitos individuales de cada instrumento que consume aire en el sistema, volumen suplementario para purgas, fugas, adiciones, etc. De lo contrario de no disponer de cifras de consumo precisas, un volumen de consumo estimado de 0,5 pies cúbicos por minuto para cada dispositivo de consumo de aire suele ser adecuado. El tanque de almacenamiento de aire debe tener la capacidad requerida para mantener esta velocidad durante aproximadamente 5 minutos o el tiempo necesario para realizar un apagado de emergencia de la planta o para cambiar a un sistema de aire de respaldo. Además, la capacidad del tanque de almacenamiento de aire debe ser lo suficientemente grande como para evitar ciclos excesivos del compresor.
Filtración y regulación: Los sistemas de aire para instrumentos normalmente están diseñados para presiones de 125 psig de resistencia y deben estar protegidos por válvulas de alivio (importante). El aire del instrumento no puede estar contaminación, como aceite, agua y cualquier gas peligroso o corrosivo (ácido sulfúrico). Se deben usar compresores no lubricados. Donde se usan compresores lubricados, se requiere un separador de extracción de aceite. La presencia de aceite puede causar contaminación del instrumento y posiblemente crear una mezcla combustible. Después de ser comprimido, el aire del instrumento debe enfriarse para eliminar la mayor parte del agua contenida. Es importante implementar un sistema de secado final para disminuir el punto de rocío del agua hasta 10 ° F por debajo de la temperatura ambiente a la presión de la línea. Se puede requerir un filtro posterior para eliminar el remanente de partículas de los deshidratadores.
Distribución adecuada: El sistema de distribución de aire debe estar libre de acumulación de líquido (bolsas). Si esto no es posible, deben instalarse válvulas de drenaje. Todas las líneas de suministro deben conectarse a la parte superior del colector de aire. Los filtros-reguladores de aire del instrumento deben estar provistos en cada dispositivo que consume aire para reducir la presión de línea a la presión de suministro recomendada por el fabricante del instrumento. Esto también proporciona una etapa más de protección contra contaminantes.
Sistemas no aéreos: Se ha usado gas natural en lugar de aire para instrumentos en algunas instalaciones remotas donde no había aire comprimido disponible. Esta práctica se debe evitar si es posible debido a problemas de seguridad y contaminación y al filtrado y limpieza adicional del gas que se debe hacer para proteger los instrumentos. El usuario debe conocer todas las regulaciones aplicables al considerar el uso de cualquier gas combustible en el servicio de instrumentación. Algunos sistemas de pequeña escala han usado nitrógeno embotellado para gas de instrumento. Esto es bastante aceptable, pero los instrumentos sin sangrado deben usarse para mantener el consumo al mínimo.
Especificaciones de fuente de alimentación
Las especificaciones del fabricante que deben tenerse en cuenta son: Regulación, Ondulación y Protección contra cortocircuitos. La regulación es una indicación de qué tan bien permanece constante la tensión de salida de la fuente de alimentación a medida que se elimina la carga eléctrica y se vuelve a conectar. Una buena regulación no implica interacción entre dispositivos conectados en la misma fuente de alimentación. Rizo es la cantidad de variación de CA en la salida de CC con una carga constante en la fuente de alimentación. Esto es especialmente crítico cuando las salidas de los transmisores están conectadas a convertidores analógico al digital en una instalación basada en computadora o microprocesador.
La ondulación de la fuente de alimentación debe ser inferior a 1/3 de esta, o que el convertidor pueda rechazar el ruido. La protección contra cortocircuitos es un medio por el cual la corriente de la fuente de alimentación está limitada a un máximo seguro en caso de que la salida se acorte accidentalmente en algún punto. Todas las fuentes de alimentación deben incluir protección contra cortocircuitos para evitar daños graves. Esta siempre deben tener el lado común de la salida separada de la tierra del chasis para permitir que el común se conecte a tierra en un solo punto a una tierra de instrumento de "alta calidad".
Fuente de poder ininterrumpida
Los sistemas de alimentación ininterrumpida (UPS), frecuentemente denominados sistemas de respaldo de batería, deben dimensionarse para abarcar el tercer tiempo de cierre si se deben mantener los niveles de suministro de energía para minimizar el comportamiento errático de la planta. Sin embargo, si el compresor de aire del instrumento es impulsado por un motor eléctrico, generalmente no es beneficioso mantener la energía de la batería más allá del tiempo en que se agota el suministro de aire. Se deben considerar todas las necesidades de instrumentos requeridas para un apagado ordenado.
El diseño de los circuitos es evitar la sobrecarga o la carga insuficiente de las baterías, así como para evitar daños a los circuitos del regulador cuando se interrumpe la entrada (CA). Inclusive se debe tener una copia de seguridad de la alimentación de CA, las baterías se utilizan para alimentar un inversor que transforma la alimentación de CC en alimentación de CA del voltaje y la frecuencia adecuados. Los interruptores estáticos están disponibles para cambiar automáticamente la entrada de la fuente de alimentación de la línea de CA normal al inversor cuando se pierde la alimentación de la línea de CA. Deben observarse las recomendaciones del fabricante para requisitos medioambientales para garantizar la fiabilidad de las fuentes de alimentación electrónicas, interruptores estáticos, etc.
Es obligatorio el mantenimiento regular de los sistemas de batería, ya que las baterías son de vida útil limitada en comparación con otros componentes electrónicos y la corrosión de la terminal puede causar problemas. Los generadores en espera pueden ser necesarios en algunas instalaciones para permitir que las operaciones del instrumento continúen más allá del límite de tiempo del sistema de la batería.
Algunos de los tipos más comunes de dispositivos de detección para la medición de variables de proceso se describen de la siguiente manera:
Sensores de presion
Manómetro: Se aplican dos presiones diferentes a dos aberturas separadas en un recipiente transparente que contiene un líquido. La diferencia en las alturas del líquido se usa como una medida de la presión diferencial. Esta diferencia se debe corregir para la temperatura y la gravedad del líquido en el manómetro (generalmente agua o mercurio).
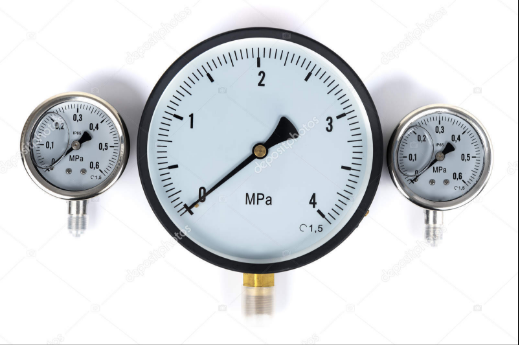
Tubos de Bourdon: Un tubo de Bourdon es una bobina metálica construida a partir de un tubo de metal que tiene la calidad elástica deseada y la resistencia a la corrosión. La tendencia del tubo a enderezarse bajo presión provoca un enlace mecánico para mover un puntero o iniciar la transmisión neumática o electrónica de la presión medida. Las trampas de condensado deben usarse aguas arriba del dispositivo en el servicio de vapor. La presión indicada es la presión "manométrica" que es relativa a la del entorno. Los medidores Bourdon también están disponibles como tipos "compuestos" que indican vacío y presión positiva.
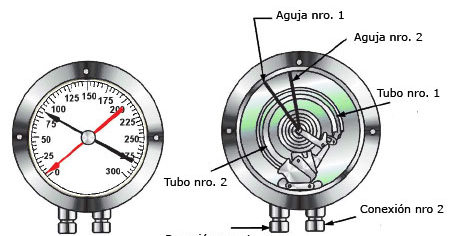
Fuelles: Un dispositivo tubular con secciones plisadas algo parecido a un acordeón. Es flexible a lo largo de su eje y se alarga o acorta de acuerdo con la presión aplicada. El fuelle se usa generalmente en servicio de baja presión o vacío, pero los tipos están disponibles para su uso con altas presiones. Los diámetros típicos van de 1/2 "a 12". A menudo se usan en transmisores de tipo balance de fuerza y otras aplicaciones donde se requieren pequeños desplazamientos. Al igual que el tubo Bourdon, indica presiones como "calibre" o relativas a su entorno.
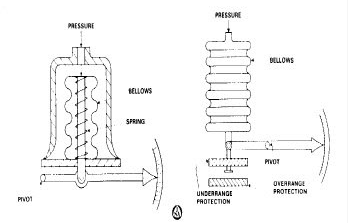
Diafragma: Un sello plano o curvo con un enlace conectado a un indicador o dispositivo de transmisión. Un diafragma puede tener sus propias propiedades de reflexión, como con un tipo metálico o puede estar unido a un muelle u otro elemento elástico, como con diafragmas no metálicos.
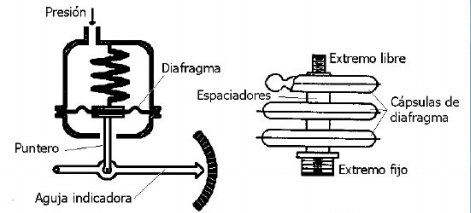
Transductores de presión eléctrica
El elemento de detección principal de muchos transductores de presión eléctrica generalmente toma la forma de un tubo de Bourdon, un fuelle o un diafragma para generar un movimiento que se transmite a un extensímetro. Un extensímetro es un dispositivo que utiliza un cable de resistencia conectado en una configuración de puente de Wheatstone para generar una señal eléctrica proporcional al movimiento y, por lo tanto, proporcional a la variable de proceso que se está midiendo.
Otros tipos de transductores de presión eléctrica usan propiedades de inductancia, capacitancia o acoplamiento magnético para convertir una medida de presión en una señal eléctrica.
Sensores de nivel
Gauge Gauge: Este es el dispositivo de nivel de proceso visual más comúnmente utilizado. Gafas de calibre generalmente se clasifican como tipos transparentes o reflejos. Un vidrio de calibre transparente consiste en un tubo de vidrio o una disposición de placas de vidrio planas en algún tipo de soporte. Dado que el nivel del fluido de proceso se ve directamente, el vidrio de calibre transparente se usa normalmente con fluidos opacos. El tipo reflejo tiene prismas reflectantes para ayudar a ver fluidos transparentes. Se debe tener precaución al manipular e instalar estos o cualquier instrumento de vidrio templado. Los arañazos o las virutas pueden reducir la resistencia del vidrio y causar problemas de seguridad.
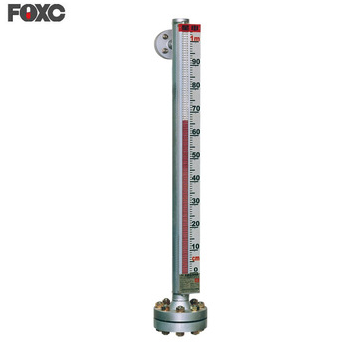
Indicadores de flotador de cadena y cinta: Se usan en tanques de almacenamiento grandes, sin presión, donde se debe medir todo el rango completo de vaciado.
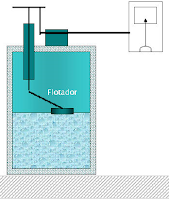
Tubo de torsión: Está unido al extremo libre de un tubo de torsión que tiene propiedades elásticas que le permiten girar al flotador. Este ligero giro del extremo libre del tubo de torsión está conectado a un indicador o transmisor. Los medidores de desplazamiento del tubo de torsión normalmente están limitados a luces de nivel de diez pies.
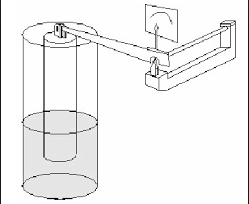
De tipo burbujeo: Se usa al vacío y a bajas presiones, y es especialmente bueno para servicios tales como azufre fundido y líquidos sucios. Este se basa en un tubo sumergido en el líquido cuyo a través se hacer burbujear aire por un rotámetro con un regulador de caudal. La presión del aire en la tubería equivale a la presión hidrostática ejercida por el líquido (método indirecto).
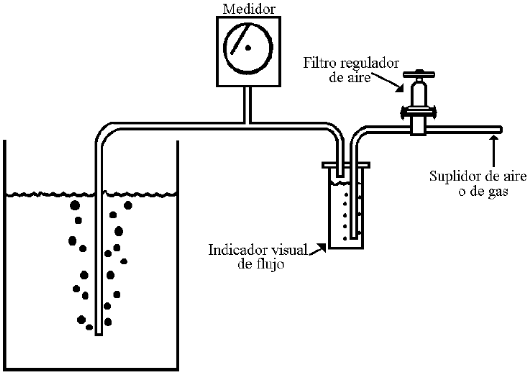
Sondas de capacitancia (no ilustradas): Método continúo de medición de nivel basado en propiedades eléctricas. Este método utiliza un electrodo colocado dentro de un vaso (o en una carcasa protectora dentro del vaso). La capacitancia entre el electrodo y la pared del recipiente o carcasa varía a medida que la constante dieléctrica varía. El dieléctrico en este caso es el fluido, por lo que la capacitancia varía en proporción al nivel del líquido. Esta capacitancia luego se mide y se convierte en una medida de nivel para indicar o transmitir.
Otros métodos de detección de niveles usan principios de:
Absorción de radiación nuclear como en un gamma gauge.
Absorción de ondas ultrasónicas.
Viscosidad del líquido.
Conductividad y expansión térmica.
Sensores de temperatura
Termopares: Consta de dos tipos diferentes de alambres (metales diferentes) unidos en un extremo para formar la unión de medición o "caliente". Donde los extremos libres están conectados al instrumento de medición, se forma una unión de referencia. Las lecturas de milivoltios medidas por el instrumento representan la diferencia en las temperaturas de las dos uniones y se pueden convertir a la temperatura por varios métodos usando datos de conversión de las tablas de termopares. Las temperaturas de referencia utilizadas normalmente para generar tablas de termopares son 32 ° F y 70 ° F.
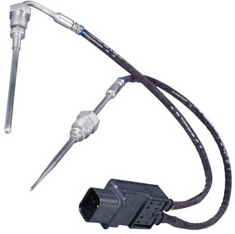
Los termopares utilizados para las mediciones de proceso generalmente están protegidos por un termopozo. La masa del termopozo debe mantenerse a un mínimo en el interés de una respuesta más rápida. El termopar debe estar en contacto térmico con el termopozo. Esto se logra mediante el uso de un lubricante térmicamente conductivo o contacto físico entre el termopar y el pozo. En muchas aplicaciones de medición y control, debe evitarse la conexión a tierra eléctrica del termopar en el punto de medición.
Termómetros de sistema lleno: Son dispositivos simples, confiables y de bajo costo. Una bombilla está conectada a un tubo capilar que está conectado a un elemento de medición (fuelles, tubo Bourdon, etc.) en un dispositivo indicador o transmisor. El sistema se llena con un líquido o gas que cambia de volumen o presión a medida que cambia la temperatura de la bombilla. La longitud de la carrera capilar es normalmente inferior a 250 pies.
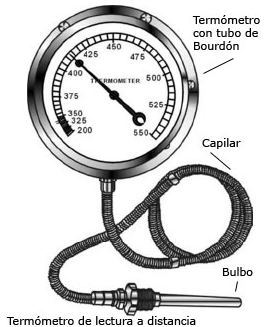
Termómetros de vástago de vidrio: Estos dispositivos se usan normalmente en la oficina, el laboratorio u otras áreas que no son de proceso. La rotura es un problema; la precisión es de 0.1 a 2.0 grados dependiendo del rango.
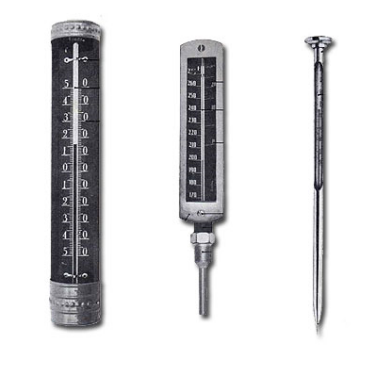
Termómetros bimetálicos: el elemento sensor consiste en dos metales con diferentes coeficientes de expansión unidos entre sí y unidos a un indicador. Estos son económicos, pero no muy precisos, y normalmente se usan en termostatos de temperatura de encendido / apagado donde no se requiere un control preciso, o en aplicaciones de proceso donde se deben monitorear cambios relativos. Deben calibrarse en o cerca del punto de operación normal de la temperatura que se monitorea.
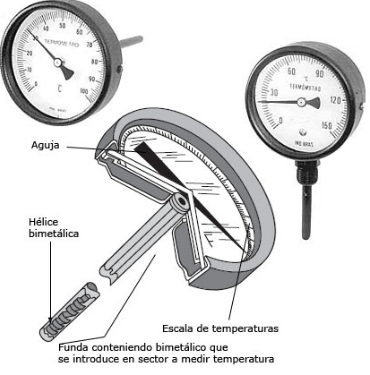
Sensores de flujo
Flujo de cabeza variable: los medidores de flujo de esta clase detectan una diferencia de presión en un elemento de flujo especialmente diseñado para crear esa diferencia de presión. El elemento de flujo más común es la placa de orificios, pero otros elementos también en uso son las boquillas de flujo, los tubos Venturi (Figura 15), los tubos Pitot, los tubos Pitot promediados, las placas diana, placa orificio (Figura 16) y los codos de tubería.
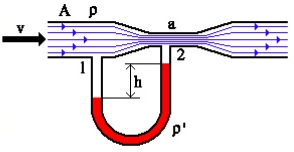
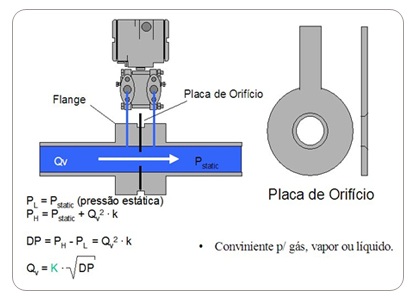
Flujo de área variable Este tipo incluye el rotámetro familiar. La presión diferencial a través del dispositivo se mantiene constante, y el área a través de la cual pasa el fluido cambia debido al movimiento del flotador hacia arriba y abajo del tubo cónico. Por lo general, estos están limitados al uso con flujos relativamente pequeños donde la indicación visual es suficiente.
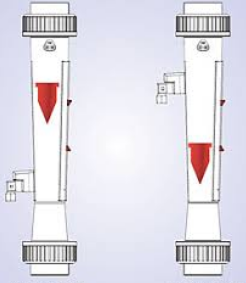.png)
Turbina: Utilizan un imán permanente montado en el tubo del medidor para crear un campo magnético. Una pequeña turbina está montada dentro del tubo y gira con una velocidad proporcional al caudal. A medida que cada paleta de la turbina pasa a través del campo magnético, se altera el flujo magnético que induce un impulso en una bobina de captación montada en la parte exterior del medidor. La frecuencia del pulso es proporcional a la velocidad de flujo. Los pulsos se cuentan y se convierten en unidades de flujo estándar.
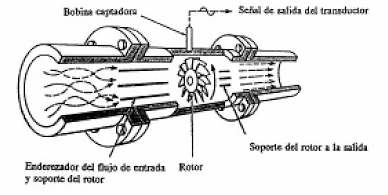.png)
Medidores de desplazamiento positivo: Los medidores de desplazamiento positivo y las bombas dosificadoras miden cantidades discretas del fluido que fluye. El elemento giratorio está acoplado mecánicamente a un transmisor o contador que integra o suma los recuentos para proporcionar una indicación en unidades de galones, litros, pies cúbicos, etc. Algunos tipos comunes son: paleta giratoria, bi-rotor, paleta giratoria, pistón oscilante y medidores de engranajes ovalados. Se utilizan para dispositivos de transferencia de custodia, como medidores de gas o bombas de gasolina.
Medidores de flujo ultrasónicos: La medición de flujo ultrasónico se basa en enviar y recibir señales acústicas a través del flujo. La diferencia en el tiempo de tránsito entre transductores, construido en lados opuestos de la tubería, da señales que pueden transferirse para fluir.
Una onda de sonido viaja más rápido con el flujo que uno propagado contra el flujo. La diferencia en los tiempos de tránsito es proporcional a la velocidad de flujo promedio del medio. Al instalar más de un par de transductores, se puede cubrir un rango más grande de los perfiles de flujo a través de la sección de medición y así aumentar la precisión del medidor.
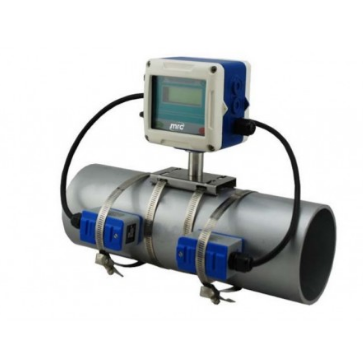
Transmisores neumáticos
Un transmisor neumático es un dispositivo que detecta alguna variable de proceso y traduce el valor medido en una presión de aire que se transmite a varios dispositivos receptores para indicación, grabación, alarma y control. El rango de señal de 3-15 psig es el estándar aceptado de la industria; sin embargo, se pueden encontrar otros rangos. Esta señal es proporcional al rango de medición de la variable de proceso.
La función primordial de un transmisor es reproducir la señal de medición de baja energía con energía suficiente para que pueda transmitirse a una distancia apreciable o utilizarse como fuente de energía para un dispositivo de control. La señal de medición de baja energía es esa posición o movimiento asociado con la acción de la variable de proceso en el elemento de detección (fuelles, diafragma, tubo de Bourdon, etc.). Los transmisores neumáticos funcionan de forma similar a los controladores proporcionales.
Transmisores electrónicos
Los transmisores electrónicos realizan la misma función que los transmisores neumáticos: una señal relacionada con el proceso de baja energía se convierte en una señal de mayor energía adecuada para conectarse a otros instrumentos en el sistema. La señal de salida de la mayoría de los transmisores electrónicos es una señal de 4-20 mA, 10-50 mA o 1-5 Vcd.
Métodos de conexión:
Es una gran preocupación para el ingeniero de instrumentos el método mediante el cual los transmisores electrónicos se conectan en el sistema de instrumentación. Las clasificaciones de "dos hilos", "tres hilos" y "cuatro hilos" a menudo se usan para describir el método de conexión. Los cuales son:
Transmisores de dos hilos: Son los más simples y económicos y se deben usar donde las condiciones de carga lo permitan. En un sistema de dos cables, la única fuente de alimentación del transmisor proviene del bucle de señal. Con referencia a la figura 4-18a, la corriente de 4 mA de "extremo cero" es suficiente para impulsar el circuito interno del transmisor y la corriente de 4 a 20 mA representa el rango de la variable de proceso medida. La fuente de alimentación y los instrumentos generalmente se montan en la sala de control.
Transmisores de tres hilos: Algunos transmisores requieren más energía de la que puede suministrar el bucle de señal (4- 20 ma, etc.) para soportar sus circuitos internos. Un cable común de CC se ejecuta desde el instrumento hasta el transmisor. Esto permite que el transmisor extraiga la potencia que necesita de la fuente de alimentación y produce la corriente de señal deseada en la salida del transmisor.
Transmisores de cuatro hilos: Algunos transmisores tienen su propia fuente de alimentación interna y no requieren conexión a la fuente de alimentación de CC. Una fuente de 120 VCA está conectada directamente al transmisor y su lazo de señal de salida está conectado solo al instrumento receptor. A menudo se usan cuando se "agrega" un instrumento a una instalación de instrumentación existente para evitar agregar a la carga de los suministros de CC. La desventaja es la necesidad de alimentación de CA en el sitio del instrumento.
Los convertidores de señal se utilizan para lograr la compatibilidad entre diferentes tipos de instrumentos o para fines de aislamiento. Algunas formas comunes de convertidores de señal son:
Aisladores: Estos suelen ser convertidores electrónicos de corriente a corriente o de voltaje a voltaje que proporcionan aislamiento eléctrico para eliminar corrientes de bucle de tierra no deseadas o voltajes de modo común.
Convertidores de señal eléctrica: Se ajustan a la misma categoría que I / Ps y P / Is porque cambian la señal de un rango a otro. Los ejemplos son 4-20 mA a 0-10 vdc, 1-5 Vdc a 10-50 mA, etc.
Convertidores de frecuencia: Los convertidores de frecuencia a CC reciben típicamente impulsos de turbinas o caudalímetros de desplazamiento positivo y proporcionan una salida proporcional de 4-20 ma, 10-50 mA o voltaje. Los convertidores de salida de voltaje a menudo se conocen como convertidores / transmisores F / V (frecuencia a voltaje). Los convertidores de V / F (voltaje a frecuencia) a menudo se usan para interconectar instrumentación de tipo "bucle de corriente" estándar para controlar dispositivos que requieren entradas de punto de consigna de frecuencia o tren de impulsos. Estos se usan comúnmente en indicadores de velocidad para equipos centrífugos de alta velocidad.
Grabadoras Un grabador es un dispositivo utilizado para trazar el valor de una o más variables medidas, generalmente en función del tiempo, pero en algunos casos contra otra variable o variables asociadas. Los grabadores a menudo se clasifican de las siguientes maneras:
De acuerdo con el uso, es decir, si la grabadora es una parte integral del sistema de medición / control o es un tipo de uso general tal como se usaría en un laboratorio o con un cromatógrafo.
Según el método utilizado para conducir el (los) bolígrafo (s): Esto se refiere a si el bolígrafo está conectado directamente al elemento de detección o a algún tipo de mecanismo de posicionamiento del bolígrafo activado por la señal de medición.
Según el tipo de gráfico: Esto se refiere principalmente a si la grabadora es del tipo de carta circular o de banda y si la unidad de eje de tiempo es alimentada por un muelle mecánico, motor eléctrico o accionamiento neumático.
Analógico o Digital: Las grabadoras analógicas son las más conocidas y las circulares. Las grabadoras digitales incluyen cosas como impresoras de banda, registradores de datos, totalizadores electrónicos y dispositivos relacionados con la computadora, como terminales de datos e impresoras.
Un indicador es cualquier dispositivo que presenta una visualización de una cantidad medida como temperatura, presión, humedad, voltaje, etc. Los indicadores se incluyen en un sistema de instrumentación como dispositivos independientes (denominados TI, PI, FI, etc.) o como parte de un dispositivo de control (TIC, PIC, etc.). Los indicadores se pueden clasificar en los siguientes grupos:
Mecánico: En estos indicadores, la cantidad medida causa el movimiento de un puntero a lo largo de una escala graduada. Este movimiento se debe a la acción de la cantidad medida en un diafragma, fuelle, bobina electromagnética u otro dispositivo sensor que está mecánicamente vinculado al puntero. Esto incluye manómetros, termómetros con esfera llena, medidores de voltaje y corriente, indicadores de nivel, etc.
Tipo de señal electrónica: Son indicadores analógicos sin partes móviles. Una señal del dispositivo sensor activa una pantalla óptica conectada a una escala graduada. Un tipo común utiliza un banco de 200 pequeños tubos llenos de gas que se iluminan aditivamente en proporción a la magnitud de la señal del proceso. Esto da como resultado una resolución del 0.5% de la escala completa.
Digital: Los indicadores digitales incluyen un convertidor analógico a digital que cambia la señal del proceso eléctrico al formato binario que luego se muestra en forma numérica. Las pantallas típicas consisten en diodos emisores de luz (LED), pantallas de cristal líquido (LCD), tubos llenos de gas, etc.
CONCEPTOS DE CONTROL
Bucles de control : Un circuito de control se conoce comúnmente como "bucle". Un bucle de control puede clasificarse como "abierto" o "cerrado" dependiendo de si los ajustes de control son ajustes manuales (bucle abierto) o determinados automáticamente por algún tipo de controlador de realimentación. (bucle cerrado).
Circuito abierto: En un sistema de control de lazo abierto, un operador realiza un ajuste manual a un dispositivo (válvula) que controla el flujo de una variable manipulada (vapor) para intentar alcanzar un cierto punto de ajuste ( valor de la temperatura deseada) de una variable controlada (agua caliente). Sin embargo, este ajuste solo es válido para las condiciones bajo las cuales el operador realizó el ajuste. Cualquier alteración, como un cambio en la temperatura del agua de entrada, la temperatura del vapor, la pérdida de calor en el entorno o el rendimiento, hará que cambie la temperatura de salida. Ver la representacion en un diagrama de bloque en la figura 21.
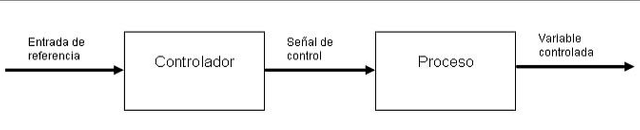
Circuito cerrado: Si se agregan los elementos de medición y control apropiados al sistema, el ciclo se cierra mediante la inclusión de un controlador automático de retroalimentación, ver figura 22. El controlador detecta cualquier diferencia entre el punto de ajuste y las señales de medición (error señal) y produce una señal de salida para conducir la válvula en la dirección correcta para ajustar la entrada de calor y hacer que la medición alcance el valor del punto de ajuste.
Control de realimentación: Los componentes básicos de un lazo de control de retroalimentación se muestran en forma de diagrama de bloques en la figura 22. El "comparador" en realidad representa el controlador completo y cualquier convertidor de señal asociado. El "elemento de control" es la válvula, el "elemento de retroalimentación" es el transmisor, y el "proceso" es la mezcla del vapor y el agua fría dentro del calentador de agua.
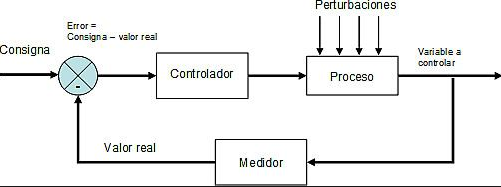
Control de avance: El control de avance de avance (a menudo llamado "control predictivo") es en realidad una forma de control de lazo abierto. Se controla una variable de entrada (temperatura del agua fría) y la variable manipulada (flujo de vapor) se ajusta en consecuencia para compensar los cambios en la variable de entrada. El control de avance casi siempre se usa junto con el control de retroalimentación para superar los efectos de alguna perturbación esperada.
Las formas básicas de acción de control o "modos" utilizados en la mayoría de los controles de proceso son: control de dos posiciones o "encendido-apagado", control proporcional, control integral o de "reinicio" y control derivado o de "velocidad". Los últimos tres modos se usan a menudo en varias combinaciones entre sí.
Controladores de dos posiciones (encendido-apagado)
La forma más simple de acción de control es el control "on-off", en el que la salida del controlador energiza o desenergiza un dispositivo de dos estados, como un relé o una válvula de tipo abierto. El controlador de dos posiciones se usa ampliamente en sistemas de calefacción y refrigeración, refrigeradores, tanques de agua caliente, compresores de aire y otras aplicaciones donde el costo de un control más preciso no está justificado. La mayoría de los controladores de dos posiciones son de acción inversa, es decir, cuando la variable medida está por encima del punto de ajuste, el controlador desactiva la variable manipulada, y cuando la variable medida está por debajo del punto de ajuste, el controlador activa la variable manipulada. Existe una "banda muerta" o brecha diferencial alrededor de la condición de error cero para minimizar el ciclo. Esto a menudo se implementa como un par de puntos de control: uno donde el controlador se "activará" y el otro donde el controlador "iniciará" en lugar de un único punto de ajuste.
Modos de control proporcional, integral y derivativo
Cuando no se puede tolerar la naturaleza cíclica del control "on-off", normalmente se usa un controlador que usa una combinación de los modos proporcional, integral y derivado. Las combinaciones normalmente usadas de estos modos son: (P) Proporcional solamente; (PI) Proporcional más integral; (PD) Derivado proporcional más; y (PID) Proporcional más integral más derivado. El modo integral rara vez se usa solo ya que agrega retraso al sistema sin los beneficios del modo proporcional. El modo derivativo nunca se usa solo ya que su salida es cero, excepto cuando la señal de error (PV - SP) está cambiando.
Controladores de acción directa y reversa
El término de la señal de error (PV - SP) indica la acción del controlador "inverso" (la salida del controlador disminuye cuando la medición aumenta). La mayoría de los controladores pueden cambiar de un tipo de acción a otro, y la elección depende de la acción del elemento de control final y de la dirección en que la variable controlada medida responde a la variable manipulada.
Modo proporcional (P)
El modo "proporcionalmente único" es el más simple de los tres modos de control. Se caracteriza por una relación lineal continua entre la señal de error (PV - SP) y la salida del controlador.
El controlador proporcional es simple, económico y no introduce retardos de tiempo adicionales en el sistema de control. Su principal desventaja es su incapacidad para hacer frente a los cambios de carga.
Modo integral proporcional Plus (PI)
El "controlador PI" es el más utilizado de los diversos tipos de controladores (70-90% de los controladores en una planta típica).
El término integral hará que la válvula (u otro elemento de control final) se mueva a una velocidad proporcional a la cantidad del desplazamiento hasta que se elimine todo el desplazamiento. La constante de tiempo integral Ti también se conoce como tiempo de reinicio, y como representa el tiempo para que la acción integral "repita" la cantidad de la acción proporcional, el recíproco de Ti (llamado "velocidad de reinicio") a menudo se da en unidades de "Repeticiones por minuto".
Modo Derivado Proporcional Plus (PD)
El control de realimentación tiene una deficiencia en cuanto a que no se toman medidas correctivas hasta que exista alguna señal de error. A menudo se encuentran problemas en el control de procesos con grandes constantes de tiempo y / o tiempos muertos. Al controlar estos procesos lentos, es necesario tomar medidas correctivas lo antes posible o el tiempo de recuperación será demasiado largo. La acción derivada se suma a la salida del controlador en función de la tasa de cambio de la señal de error (PV - SP). Esto también se llama acción de control de "velocidad" o "preactividad", y el control que utiliza acción derivada (velocidad) se conoce como control "anticipatorio".
La constante de ganancia derivada Kd se puede expresar como Kd = KpTd. La constante de tiempo derivada Td representa el tiempo requerido para que la contribución del término derivado sea igual a la contribución del término proporcional con una señal de error en constante cambio o "rampa". La derivada es, por su naturaleza, sensible al ruido de la señal y puede causar desgaste excesivo en la válvula de control. Se debe hacer un filtrado de señal suficiente para reducir el ruido cuando se usa acción derivada en el controlador.
Modo derivativo proporcional Plus Integral Plus (PID)
Muchos controladores incluyen circuitos para modos proporcionales, integrales y derivados que permiten al usuario seleccionar la acción de control deseada.
Seleccionar la válvula de control adecuada para cada aplicación implica muchos factores. El diseño del cuerpo de la válvula, el estilo del actuador y la característica del tapón son elementos críticos para la selección. El dimensionamiento correcto de la válvula es necesario para un control del proceso preciso, eficiente y económico. En áreas donde el personal se verá afectado, la predicción y control del ruido se convierte en un factor importante.
Las pautas de aplicación de ingeniería, los nomogramas y las ecuaciones que se presentan en las siguientes páginas pueden usarse para determinar la configuración correcta de la válvula de control, el tamaño y las características de flujo, y para predecir niveles de ruido para la mayoría de las aplicaciones. El material presentado aquí también se puede usar para evaluar el rendimiento de las válvulas instaladas en plantas existentes.
Las ecuaciones dadas en esta sección se usan para calcular el coeficiente de flujo (Cv o Cg) requerido para que una válvula pase el flujo requerido. La mayoría de los fabricantes de válvulas publica coeficientes de flujo para cada estilo y tamaño de válvula. En la figura 23 se presenta una breve descripción de los dos componentes principales de una válvula de control, el cuerpo de la válvula y el actuador.
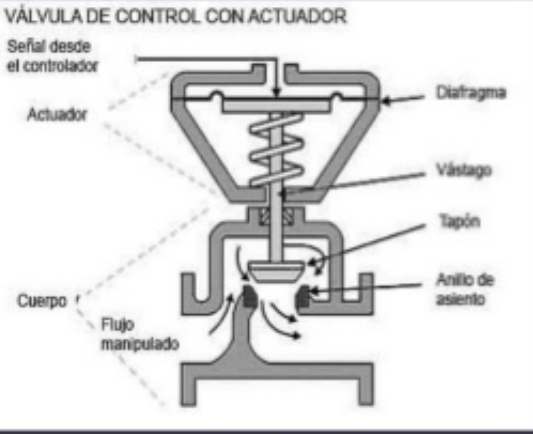
Cuerpos de control de válvula
El cuerpo de la válvula de control regula la velocidad del flujo de fluido a medida que la posición del tapón de la válvula se cambia por la fuerza desde el actuador. Por lo tanto, el cuerpo de la válvula debe permitir la transmisión del empuje del actuador, resistir los efectos químicos y físicos del proceso y proporcionar las conexiones finales apropiadas para acoplarse con la tubería adyacente. Debe hacer todo esto sin fugas externas. La mayoría de los diseños de cuerpo de válvula son del estilo de globo, pero otras configuraciones como estilos de bola y mariposa están disponibles. La selección final depende de la revisión detallada de la aplicación de ingeniería.
Actuadores de válvula de control
Los actuadores de válvula de control operados neumáticamente son el tipo más popular en uso, pero los actuadores eléctricos, hidráulicos y manuales también son ampliamente utilizados. El actuador neumático de resorte y diafragma se especifica comúnmente, debido a su confiabilidad y su simplicidad de diseño. Los actuadores de pistón operados neumáticamente proporcionan una capacidad de posicionador integral y una alta potencia de fuerza para condiciones de servicio exigentes, tales como como alta presión diferencial o larga distancia de recorrido del vástago de la válvula.
Discusión de las características de flujo y selección de válvula
La característica de flujo de una válvula de control es la relación entre la velocidad de flujo a través de la válvula y el recorrido de la válvula, ya que el recorrido varía de 0 a 100%. La "característica de flujo inherente" se refiere a la característica observada durante el flujo con una caída de presión constante a través de la válvula. La "característica de flujo instalado" se refiere a la característica obtenida en servicio cuando la caída de presión varía con el flujo y otros cambios en el sistema.
La figura 24 ilustra las curvas características de flujo típicas. La característica de flujo de apertura rápida proporciona un cambio máximo en la tasa de flujo en el recorrido de la válvula baja con una relación bastante lineal. Incrementos adicionales en el recorrido de la válvula producen cambios bruscamente reducidos en la velocidad de flujo. Cuando el obturador de la válvula se acerca a la posición abierta, el cambio en la tasa de flujo se aproxima a cero. En una válvula de control, el tapón de la válvula de apertura rápida se utiliza principalmente para el servicio de encendido y apagado; sin embargo, también es adecuado para muchas aplicaciones donde normalmente se especificaría un tapón de válvula lineal.
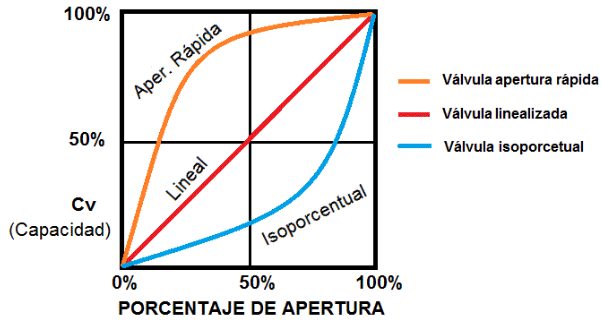
La curva de característica de flujo lineal muestra que el caudal es directamente proporcional al recorrido de la válvula. Esta relación proporcional produce una característica con una pendiente constante de manera que con una caída de presión constante (ΔP), la ganancia de la válvula será la misma en todos los flujos. (La ganancia de la válvula es la relación de un cambio incremental en la velocidad de flujo a un cambio incremental en la posición de la válvula. La ganancia es función del tamaño y la configuración de la válvula, las condiciones de operación del sistema y la característica del tapón de la válvula). para el control de nivel de líquido y para ciertas aplicaciones de control de flujo que requieren ganancia constante.
En la característica de flujo de igual porcentaje, los incrementos iguales del recorrido de la válvula producen iguales cambios porcentuales en el flujo existente. El cambio en la velocidad de flujo siempre es proporcional al caudal justo antes de que se realice el cambio de posición para un tapón de válvula, disco o posición de bola. Cuando el tapón, disco o bola de la válvula está cerca de su asiento y el flujo es pequeño, el cambio en la velocidad de flujo será pequeño; con un flujo grande, el cambio en la velocidad de flujo será grande. Las válvulas con una característica de flujo de porcentaje igual se usan generalmente para aplicaciones de control de presión. También se usan para otras aplicaciones en las que un gran porcentaje de la caída de presión total del sistema normalmente es absorbida por el sistema, con un porcentaje relativamente pequeño de la válvula de control. Las válvulas con una característica de porcentaje igual también deben considerarse cuando se pueden esperar condiciones de caída de presión altamente variables.
La curva característica de flujo parabólico modificado se encuentra entre la curva lineal y la curva de igual porcentaje.
Computadoras analógicas
Una computadora analógica de control de proceso está compuesta de módulos electrónicos tales como amplificadores, veranos, controladores, multiplicadores, divisores, dispositivos de raíz cuadrada y cuadrada, módulos de adelanto y retraso, limitadores y dispositivos especiales de tiempo muerto. Estos módulos se basan en el amplificador operacional de circuito integrado y están interconectados para implementar la estrategia de control deseada. La computadora analógica de control de proceso es muy confiable, de bajo costo y fácil de usar, pero se ha vuelto obsoleta hasta cierto punto gracias a la computadora digital más versátil.
Computadoras digitales
Las computadoras digitales son atractivas para muchas aplicaciones en el campo de control de procesos debido a su velocidad, precisión, flexibilidad, capacidad de visualización y registro, y capacidad para realizar cálculos complejos y almacenar y transmitir grandes cantidades de datos.
Las computadoras digitales vienen en casi cualquier tamaño o forma, desde diminutos dispositivos de una sola tarjeta para propósitos especiales hasta grandes computadoras de procesamiento de datos.
Controladores lógicos programables (PLC): Clase especial de microordenadores diseñados para implementar una serie de funciones secuenciales tales como diagramas de red de escalera. Son los más adecuados para operaciones de tipo lote o control de máquina. Algunos ejemplos son: control de deshidratación, control de carga del compresor, secuenciadores de arranque del motor y mezcladores de producto.
Microordenadores: Los microordenadores generalmente incluyen un sistema de software de nivel más alto y un hardware de entrada / salida más versátil que los PLC. A menudo se usan como la computadora de control de procesos en instalaciones pequeñas o medianas, como plantas de gas.
Miniordenadores: El miniordenador incorpora una unidad lógica aritmética más compleja y de mayor velocidad que el procesador central. Los miniordenadores admiten grandes cantidades de memoria y pueden incluir una unidad de disco de alta velocidad para almacenamiento de datos y programas, así como puertos de entrada / salida para interactuar con una variedad de equipos periféricos. Los miniordenadores se usan normalmente como la computadora de control de procesos en instalaciones más grandes, como refinerías, plantas químicas, etc.
Además del conjunto de impresoras, terminales CRT, unidades de disco, etc., que normalmente se encuentran en un sistema informático, existe un sistema de entrada / salida de proceso. La mayoría de las señales de entrada y salida de proceso pertenecen a uno de los siguientes grupos:
Analógico (flujos, presiones, niveles, temperaturas, etc.)
Digital (sentido de activación / desactivación de estado) • Pulso (tacómetros, contadores, etc.)
Serie (datos codificados)
Analizadores cíclicos
Generalmente los instrumentos analíticos son dispositivos de datos cíclicos. Estos toman automáticamente una muestra de la secuencia de proceso, la analizan y transmiten los resultados al dispositivo deseado. Como la mayoría de los ciclos tardan de uno a 20 minutos en completarse, se introduce un "tiempo muerto" considerable en un lazo de control utilizando este tipo de medición. La compensación de tiempo muerto debe incluirse en el esquema de control para una respuesta de control adecuada. El muestreo de flujo de proceso es un elemento de vital importancia en una buena cromatografía o con cualquier técnica de análisis. Algunos puntos de consideración son:
Sonda de muestra: debe ubicarse en un punto del proceso donde el material a analizar esté en la fase deseada (vapor o líquido) a presión y flujo suficientes.
Líneas de muestra: Deben mantenerse lo más cortas posible para un tiempo de transporte mínimo. Puede ser necesario rastrear el calor para evitar que las muestras de vapor se condensen. El flujo de muestra debe ser lo suficientemente grande como para vaciar completamente la línea entre ciclos de análisis.
Filtros de muestra: Se usan para mantener cualquier materia particulada fuera del analizador. Se pueden requerir recipientes extraíbles u otros dispositivos para eliminar el condensado líquido.
Bombas de muestra: Requeridas para ciertos procesos de baja presión. Los aspiradores de vacío pueden usarse para flujos de muestra bajos.
Otros instrumentos de tipo cíclico o por lotes determinan cantidades tales como presión de vapor, punto de rocío, punto final, punto de inflamación, contenido de Btu y contenido de azufre.
Analizadores Continuos
Otros instrumentos analíticos realizan análisis continuos de una corriente de proceso para un parámetro específico, como el contenido de oxígeno, la densidad del gas, etc.
Algunos analizadores continuos bombean o hacen fluir una muestra a través de una celda detectora. Otros colocan el elemento detector directamente en la secuencia de proceso. Los métodos de detección varían ampliamente y pueden incluir el uso de radiación nuclear, óptica, lengüetas vibratorias, celdas de flotación, "quemadores" catalíticos y otros métodos.
Diagrama de control del sistema
Los especialistas ( Ing. de proceso) especifican el proceso a través del desarrollo de los Diagrama de tuberías e instrumentación, como se ilustra en la figura 25. No obstante, los ingenieros de proceso representan el comportamiento total de la planta. Sin embargo, Diagramas de flujo de procesos (figura 26) proporcionan instalaciones limitadas para la documentación de la funcionalidad general y los aspectos operativos de la planta.
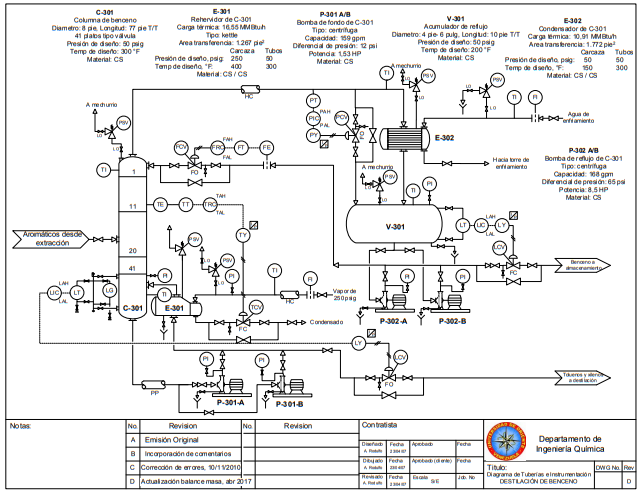
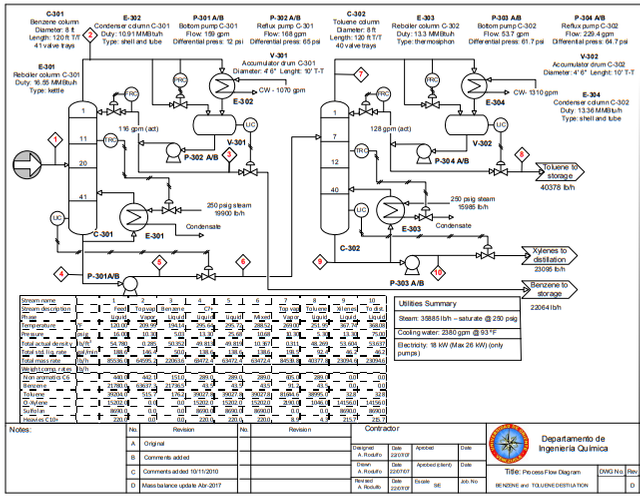
El trabajo del ingeniero del sistema de control es diseñar el sistema de control con el propósito de la funcionalidad del proceso requerida para lograr las especificaciones del producto, tales como los requisitos impuestos por la filosofía general de operación y control y los niveles de personal.
La eficiencia operativa de la planta es muy importante, difícil sin la documentación adecuada de las funciones generales de control y monitoreo disponibles por esta misma razón el ingeniero debe comprender cada proceso. A menudo, los problemas operacionales dentro de los diferentes sistemas no se pueden identificar hasta que el sistema esté en funcionamiento, lo que lleva a modificaciones importantes en las últimas fases del proyecto. Con el fin de obtener una comprensión común de la funcionalidad del sistema de control entre todas las partes involucradas en una etapa inicial del proyecto, se han introducido Diagramas de control del sistema.
Espero que le guste mi post. ¡Saludos!
Muchas gracias. Completamente agradecido por el apoyo, me motiva a escribir contenidos de calidad. Cada esfuerzo tiene su fruto.
¡Un fuerte abrazo!
Wow!
Buena publicación.
Sin embargo, no parece que estés recibiendo la valoración a tu post que mereces. Deberías echarle un vistazo a proyectos de curación serios que reconozcan tu esfuerzo. Te sugiero la comunidad de @proconocimiento.
Suerte...
Congratulations! This post has been upvoted from the communal account, @minnowsupport, by nilsonnavarro from the Minnow Support Project. It's a witness project run by aggroed, ausbitbank, teamsteem, theprophet0, someguy123, neoxian, followbtcnews, and netuoso. The goal is to help Steemit grow by supporting Minnows. Please find us at the Peace, Abundance, and Liberty Network (PALnet) Discord Channel. It's a completely public and open space to all members of the Steemit community who voluntarily choose to be there.
If you would like to delegate to the Minnow Support Project you can do so by clicking on the following links: 50SP, 100SP, 250SP, 500SP, 1000SP, 5000SP.
Be sure to leave at least 50SP undelegated on your account.
Mira me encanta que hayan más personas interesadas por el área de la ingeniería y especificamente por la automatización y la instrumentación, la instrumentación es INDISPENSABLE si se quiere automatizar, si se quiere controlar alguna variable o proceso, por eso me agrada muchisimo tu iniciativa, sin embargo te sugiero que hagas post más cortos, hay mucha tela que cortar. Mucho éxito y saludos.
Hola! Muchas gracias por tu sugerencia, lo tomare en cuenta. ¡Saludos!
Esto es toda una clase amigo, te felicito por tanto esfuerzo y dedicación en pro de compartir conocimientos que en lo personal me apasionan, tengo una fascinación por la Automatización y esto es una clase para mi. Sin embargo; te doy la misma sugerencia de la amiga @betzabesp94, si recortas este contenido y lo fragmentas y varios post tendrás mucho material para varios días, saludos!
Muchas gracias amigo por la sugerencia. Esto es parte de mi carrera que estudio y me gusta mucho. Me alegra que se tomo el tiempo en leerlo. ¡Saludos! @efren.arnaude