Controladores de Filtrado - QC Drill Starch:
Son agentes que disminuyen la cantidad de agua que pasa hacia la formación permeable cuando el lodo es sometido a una presión diferencial. El filtrado se controla a través de dos mecanismos diferentes: primero, mediante la formación de un revoque poco permeable y segundo, incrementado la viscosidad de la fase líquida. Este incremento se logra mediante el uso de diferentes polímeros. Además agrega que, los materiales más utilizados para controlar filtrado son: bentonita, polímeros manufacturados, almidones y adelgazantes orgánicos.
Los productos controladores de filtrado tienen como objetivo primordial minimizar la invasión de filtrado del fluido hacia las formaciones permeables, de la misma manera su causa principal es debido a la presión diferencial ejercida por la columna hidrostática dentro del hoyo, destacan además que uno de los principales productos empleados es el almidón.
En este sentido, el QC Drill Starch es un producto químico diseñado para controlar la perdida de filtrado en fluidos Base Agua, en especial en Drill In empleados durante la construcción del hoyo de producción. Es mismo no es más que un almidón resistente a altas temperaturas, además cumple otras funciones como inhibir arcillas actuando como agente encapsulante, entre sus principales propiedades se cuenta con una elevada resistencia a ataque de bacterias, efectivos en fluidos pesados.
Del mismo modo, los polímeros son productos químicos efectivos para minimizar la perdida de filtrado hacia la formación, conformados por almidones naturales o celulosa modificada a polímeros sintéticos.
Los polímeros usados en los fluidos de perforación pueden ser clasificados de tres maneras. Se pueden clasificar de acuerdo a su química, es decir iónica o no iónica; de conformidad con su función, tal como viscosificadores o aditivos de control de filtración; o simplemente de acuerdo con su origen. Es importante resaltar que el producto QC Drill Starch se considera un polímero natural.
Condiciones Actuales:
Cuando se desarrolla la etapa de planificación y diseño para la construcción de un pozo es necesario estudiar las condiciones del área donde se realizara este tipo de trabajo con la finalidad de establecer las mejores prácticas operacionales que permita minimizar los tiempos y costos improductivos. Uno de los aspectos a considerar son las condiciones geológicas del campo, resaltando las relacionadas con la estratigrafía y estructuras, gradientes de presión y temperatura, permeabilidad, sedimentología, así como su evaluación petrofísica, aspectos necesarios para elaborar el programa de trabajo, incluidos la formulación más apropiada para los fluidos de perforación.
Temperatura:
La temperatura no es una medida de "calor en el cuerpo", la temperatura es una magnitud física que indica cuantitativamente, el estado de "caliente" o "frío" de un cuerpo, se expresa mediante un número asociado convencionalmente al cuerpo. Ahora bien, relacionado esta propiedad a las capas o estratos de subsuelo es un parámetro esencial el cual se debe conocer al momento de formular un fluido de perforación, ya que permitirá seleccionar los mejores productos químicos para dar cumplimento a sus funciones, principalmente en aquellos que refuercen la formación de un revoque para minimizar la perdida de filtrado en zonas productoras muy calientes.
Presión:
La presión es la fuerza por unidad de área que ejerce un fluido, en la industria petrolera se manejan diferentes tipos de presión, así como: presión de formación, presión de fricción, presión de fractura y presión hidrostática. La presión de formación, es la ejercida por el contenido de líquido o gas en los espacios porales de la formación, esa presión puede ser afectada por el peso de la sobrecarga por encima de la formación, que ejerce presión tanto sobre los fluidos contenidos en los espacios vacíos de la roca como sobre los granos.
Por consiguiente, la presión de fricción es la cantidad de fuerza que se utiliza para superar la fricción. La presión de fractura es la cantidad de presión que se necesita para deformar de modo permanente (falla o agrietar), la estructura rocosa de la formación. Y la presión hidrostática es la presión total del fluido en un punto dado del pozo. Es por ello que el conocimiento que se tenga sobre las presiones de formación es de suma importancia para definir la densidad o peso de los fluidos de perforación empleado en toda y cada una de las fases de construcción de un hoyo, lo que permitiría construir las curvas de densidades evitando tanto el sobrebalance extremo (fracturaría la formación) o bajo balance (arremetida) con sus respectivos márgenes de seguridad. Es decir, controlar la energía presente en el medio poroso a través de los fluidos (gas, petróleo y gas).
Permebilidad:
Es la medida que indica la capacidad de una roca para transmitir un fluido monofásico bajo condiciones de flujo laminar. La unidad de permeabilidad es el Darcy. Del mismo modo, es una propiedad del medio poroso que cuantifica la capacidad de un material para trasmitir fluidos (en otras palabras es una medida de la conductividad de un medio poroso para un fluido). La permeabilidad está referida a su capacidad de permitir el flujo de fluidos a través del sistema de poros interconectados.
Es importante destacar que esta propiedad es sumamente importante estudiarla ya que de ella depende la producción de petróleo y gas en un pozo, por ende, una alteración en ella causaría un daño u obstrucción de los conductos. Evidentemente, esta zona de interés debe cuidarse durante la perforación de un hoyo a través de un revoque que reúna condiciones ideales para evitar la invasión de filtrado.
Petrofísica:
Es la especialidad que caracteriza las propiedades físicas de las rocas, mediante la integración del entorno geológico, perfiles de pozos, análisis de muestras de roca y sus fluidos, propiedades e historias de producción. Del mismo modo, la caracterización petrofísica de yacimientos consiste en evaluar cualitativa y cuantitativamente una formación de acuerdo a modelos determinados. Además, para llevar a cabo esta evaluación, se requiere necesariamente de un trabajo multidisciplinario sustentado en un proceso sistemático e integral, en donde la integración, la conjugación de resultados y flujo de información son fundamentales. El nivel de conocimientos y la experiencia también representan un punto de impacto; sin dejar de mencionar los procedimientos técnicos así como también las herramientas de análisis, donde la definición de objetivos y alcances, así como la base de información deben ser suficientemente confiables. En este sentido ambos autores coinciden en la importancia de evaluar las rocas almacenadoras de hidrocarburo con la finalidad de identificar las más prospectivas a ser perforadas.
Estratigrafía:
La Estratigrafía puede definirse como el estudio de las sucesiones de roca y la correlación de eventos y procesos geológicos en tiempo y espacio”. Cabe agregar, que estos últimos hacen mención que la paleontología o estudio de fósiles es parte esencial de la misma. Es importante mencionar que conocer la estratigrafía del área donde se perforaran pozos es de vital importancia debido que a través de ella se seleccionan los diversos sistemas de fluidos de perforación para contrarrestar cualquier problema con algún tipo de roca o formación, por ejemplo lutitas hinchables o geopresurizadas.
Problemas Operacionales:
Son aquellos subsistentes durante el proceso de la perforación de pozos, para la prevención de los mismos se toman en cuenta los problemas ocurridos en pozos vecinos para realizar el programa del pozo a perforar, para así poder determinan las acciones a tomar de manera preventiva y planes de contingencias para cualquier eventualidad durante el proceso. En este sentido se deben preparar fluidos de perforación que permitan minimizarlas, consigo disminuir los tiempos y costos improductivos, asi como también minimizar sus efectos sobre la formación de interés productor.
Durante las operaciones de perforación a pozos ocurren una serie de problemas que afectan la operatividad de las mismas, causando incremento de los tiempos y costos no operativos. Es por ello que, es de vital importancia estar familiarizados con estos para estar preparados y solventarlo de la mejor manera posible, cabe mencionar que cuando ocurren estos imprevistos la experiencia y el sentido común de la cuadrilla de trabajo resuelven el problema una vez que se halla identificado aplicando una serie de acciones. Además, se deben registrar todos los parámetros de perforación antes, durante y después. Sin los registros de la tendencia o sin la secuencia de los eventos, muchos de estos no van a ser fáciles de solventar debido a su nivel de complejidad.
Los principales problemas operacionales donde una tubería pegada involucra la imposibilidad de mover la sarta de perforación hacia adentro o hacia afuera del pozo y una consecuente interrupción en las operaciones programadas, causadas por las fuerzas de arrastres excesivas. Una vez que la tubería se pega el costo de despegarla y volver a trabajar puede exceder la cantidad presupuestada para las operaciones llevadas a cabo. Es importante destacar que este tipo de problema se genera por diversas causas, tales como: empaquetamiento, cambio de geometría de hoyo, limpieza ineficiente del anular, alto diferencial hidrostático entre el fluido y revoque, entre otros.
En sincronía con los anteriormente expuesto, el hecho que durante la construcción de un pozo se presentan múltiples problemas operacionales los cuales afectan significativamente los costos y tiempos operacionales, sin embargo existe uno muy particular, no es más que la formación de un revoque grueso y esponjoso afectando directamente la permeabilidad de la rocas, por ende, la productividad del pozo. Adicionalmente, crea una reducción en el diámetro del hoyo pudiéndose atascar la sarta de perforación. Es por ello que, se debe controlar efectivamente la generación de este puenteo mecánico mediante controladores de filtrado más eficiente, seguros y confiable como el estudiado en la presente investigación.
Hoyo Reducido:
Se hace referencia a un hoyo reducido o Slim Hole cuando se está formando un revoque grueso y esponjoso debido a la mala calidad de los controladores de filtrados empleados para la formación del bloqueo mecánico de las gargantas porales, además de la excesiva presencia de sólidos indeseados minimizando consigo el diámetro real del hoyo, incluso por debajo del diámetro de la mecha empleada. De la misma manera, se incrementa la posibilidad que la sarta de perforación se atasque.
Perdida de Filtrado:
Durante las operaciones de perforación y/o reparación de pozos, cuando se circula el fluido o se mantiene en condiciones estáticas. Por efecto del diferencial de presión hacia la formación y la permeabilidad de esta, se pierde fluido a la formación permeable, formándose un revoque en la cara de esta, por la filtración de las partículas sólidas contenidas en el fluido. La filtración ocurre bajo condiciones tanto estáticas como dinámicas, durante las operaciones de perforación en cualquier fase.
Es el volumen líquido forzado a través de un medio poroso durante el proceso de filtración. El filtrado indica la cantidad relativa de líquido que se filtra a través del revoque hacia las formaciones permeables cuando el fluido es sometido a una presión diferencial. Esta propiedad, afectada por la presión, la dispersión, la temperatura y el tiempo, se controla en formaciones permeables no productoras con sólidos arcillosos comerciales que forman revoques finos y de baja permeabilidad y con aditivos reductores de filtrado. En formaciones productoras el control se hace con sólidos dimensionados que constituyen sellos efectivos y con agentes reductores de filtrado.
Formación de revoque. Fuente: Prieto (2007)
Pega o Atascamiento de Tubería
Una tubería pegada involucra la imposibilidad de mover la sarta de perforación hacia adentro o hacia afuera del pozo y una consecuente interrupción en las operaciones programadas, causadas por las fuerzas de arrastres excesivas. Una vez que la tubería se pega el costo de despegarla y volver a trabajar puede exceder la cantidad presupuestada para las operaciones llevadas a cabo. Si se toma la decisión de soltar la tubería en algún punto, o si la tubería se parte, hay generalmente menos de un 50% de posibilidades de pescarla en el hoyo.
Adicionalmente, la mayoría de los incidentes de tubería pegada suceden alrededor de los cambios de cuadrilla que en otras horas del día. Generalmente estos incidentes ocurren dos horas antes o dos horas después del cambio de cuadrilla. Se recomienda cuando se cambia el turno llenar el formato que lleva el mismo nombre y así reducir las posibilidades de error humano. Del mismo modo, algunas veces la sarta de perforación se pega en el pozo como resultado de factores que van más allá del control de la cuadrilla del equipo.
Es por ello, que en estos casos es causado por el programa específico del pozo (incluye complejas y difíciles operaciones) combinados con los estratos geológicos que se van a perforar. Las formaciones móviles o la intercalación de estratos de diferente dureza, permeabilidad, presión y las formaciones falladas son todas condiciones que aumentan el potencial de tubería pegada. De igual forma, es posible que el equipo de perforación y sus herramientas sean inadecuados para el trabajo.
La pega de tubería representa uno de los problemas de perforación más comunes y más graves. La gravedad del problema puede variar de una inconveniencia menor que puede causar un ligero aumento de los costos, a complicaciones graves que pueden tener resultados considerablemente negativos, tal como la pérdida de la columna de perforación o la pérdida total del pozo. Un problema de pegadura podría ser agravado fácilmente por una reacción inapropiada. Una evaluación de los sucesos que resultaron en la pegadura de la tubería indica frecuentemente la causa más probable y puede llevar a medidas correctivas apropiadas. En general, la tubería se pega mecánicamente y por presión diferencial.
Pega de tubería causada por derrumbe o ineficiencia de limpieza en hoyo.
Tomado del Manual de Samán, Tecnología Integral en Petroleó, S.A. (2010)
Pérdida de Circulación
Una pérdida de circulación se produce cuando la presión hidrostática excede la resistencia de la formación. Las presiones altas también pueden ser el resultado de las malas prácticas de bajada de tubería, fluido muy denso, excesiva viscosidad o malas prácticas de perforación. Esta pérdida se manifiesta por una reducción total o parcial en el volumen de los retornos de los fluidos del pozo en comparación con el volumen bombeado pozo abajo, resultando una disminución en los tanques.
La pérdida de circulación de flujo se determina mediante indicadores de volumen en los tanques o por medio del tanque de viaje si se está sacando o bajando tubería. Dependiendo de la magnitud del volumen de pérdida de fluido las operaciones de perforación pueden verse afectadas. Si el espacio anular del pozo no se mantiene lleno, incluso cuando ha cesado la circulación del fluido, la presión hidrostática disminuirá hasta igualar a cero la presión diferencial entre la columna de fluido y la zona de pérdida. Esto pude incluir a los fluidos de formación de otras zonas, controladas anteriormente por la presión hidrostática del fluido, a fluir dentro del pozo, dando resultado una surgencia o arremetida y en caso extremo un reventón subterráneo. También puede causar el derrumbe al interior del pozo de formaciones anteriormente estables, atrapando y pegando la tubería.
Concentraciones
Se hace referencia a la concentración de un producto químico empleado en la formulación de un fluido de perforación, en el caso particular de la presente investigación se relaciona a la cantidad de producto controlador de filtrado expresada en libras por cada barril a preparar necesarios para garantizar el puenteo mecánico o obturación de la garganta poral para minimizar la invasión de filtrado, especialmente cuando se trata de la zona productora o interés, con la finalidad de no afectar su permeabilidad, por ende minimizar el daño de formación.
Reología
Reología (del griego reos, fluir y logos, estudio) es la ciencia del flujo y la deformación de la materia, describe la interrelación entre fuerzas, deformaciones y tiempo. La reología es aplicable a todos los materiales, desde los gases hasta los sólidos. La ciencia de la reología tiene apenas 80 años, fue fundada por dos científicos en los años veinte quienes tuvieron la necesidad común de describir las propiedades de flujo de fluidos. Estos pioneros fueron los profesores Marcus Reiner y Eugene Bingham. Traducido a términos reológicos esto significa que si se espera tiempo suficiente todo fluirá.
La reología de fluidos es usada para describir la consistencia de diferentes fluidos, normalmente mediante dos componentes, la viscosidad y la elasticidad. Por viscosidad se entiende la resistencia a fluir o el “espesamiento” y por elasticidad la “pegajosidad” o “estructura”.La reología es entonces la rama de la física que estudia el comportamiento de los fluidos sometidos a diferentes tipos de esfuerzos.
Es por ello que, a través de varias propiedades reologicas tales como: viscosidad de embudo y plástica, punto cedente, resistencia de gel, entre otros el ingeniero de campo puede definir su comportamiento a través de unas ecuaciones denominadas modelos reologicos, logrando estimar las caídas de presión en las diferentes geometrías, considerando adicionalmente la velocidad promedio y longitudes de tubería.
Filtrado API
Es la medición del comportamiento de filtración y las características de la formación de paredes de un fluido de perforación son fundamentales para el control y tratamiento los fluidos, así como las características del filtrado como petróleo, agua o emulsiones. Estas están afectadas por el tipo y cantidades de sólidos en el fluido y sus interacciones físicas y químicas, las que a su vez, son afectadas por la temperatura y la presión.
Hay que destacar que los resultados obtenidos en esta prueba no son tan certeros con el solo hecho de utilizar valores de presión y temperatura de 100 lpc y ambientes respectivamente muy lejos de las condiciones reales del hoyo donde se forma el revoque durante la perforación de pozos, sin embargo, su filtrado ayuda a realizar pruebas químicas necesarias para medir el nivel de contaminación dentro del mismo.
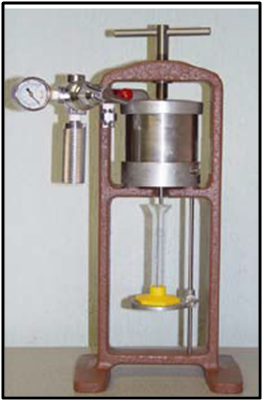
Filtración AP-AT
Consiste en medir el fluido filtrado, en mililitros, a través de un papel de filtro Whatman 50, o equivalente o en su defecto Dynallo X-5, o disco poroso equivalente, calculando el área a 7,1 + 0,1 plg2 de diámetro, durante 30 minutos manteniendo un diferencial de presión de 500 loca a una temperatura mayor que la ambiental. Básicamente esta prueba es la que maneja valores más reales en cuanto a las condiciones del hoyo relacionados con presión y temperatura.
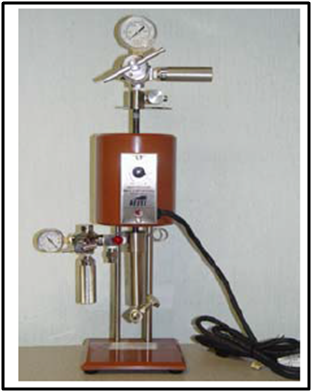
)
Potencial de Hidrogeno (pH)
La abreviatura pH significa potencial del ion hidrógeno e indica el grado de acidez o basicidad de una solución acuosa. La escala de pH va de cero (0) a catorce (14), siendo siete (7), el valor correspondiente a un pH neutro. Valores menores de siete (7), son índices de acidez y mayores de 7 de alcalinidad. El pH no determina el iono los iones responsables de la acidez o la alcalinidad del lodo, debido a que acidez y alcalinidad no es lo mismo a pesar de estar estrechamente relacionadas.
El conocimiento de la relación entre pH y alcalinidad es un factor primordial en la determinación de los diferentes contaminantes de un fluido de perforación. El pH se expresa como el inverso del logaritmo base 10 de la concentración de iones de hidrógeno o, lo que es igual, al logaritmo negativo de esa concentración. Esto quiere decir que una solución de pH 11 es 10veces mas básica que una que tenga pH 10 y es 100 veces más básica si el pH fuese de 9 ósea alcalino.
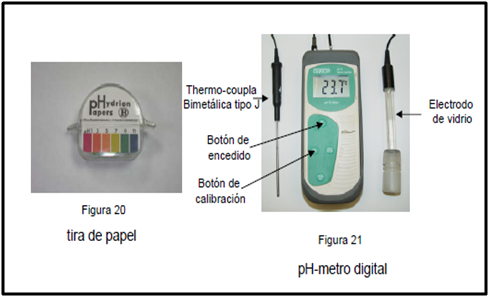
Figura 5. Métodos para determinar el pH.
*Tomado de Prieto (2007)*
La medición del pH de un fluido de perforación (o de filtrado) y el ajuste del mismo son fundamentales para el control de los fluidos de perforación. Interacciones con las arcillas, solubilidad de varios componentes y contaminantes, así como la efectividad de los aditivos son todos dependientes del pH, el control de procesos de corrosivos por ácidos y sulfuros.
El método recomendado para la medición del pH de un fluido de peroración es con un phmetro con electrodo de vidrio. Este método es certero y da valores de pH confiables, libres de interferencias si el sistema de electrodos es de Buena calidad y se usa con un equipo diseñado correctamente. Existen equipos que compensan automáticamente la sensibilidad (slope o pendiente), según la temperatura y son preferidos sobre los instrumentos que se ajustan manualmente. Es evidente que ambas fuentes destacan la importancia de mantener dentro de valores óptimos esta propiedad con el fin de evitar que el fluido de perforación sea corrosivo, por ende dañar los diversos equipos.
Contenido de Líquidos y Sólidos
Los porcentajes líquidos y sólidos de un fluido de perforación base agua o aceite, se calculan en una retorta de lodo con capacidad de 10, 20 y/o 50 cc. El funcionamiento de una retorta se basa en un proceso de destilación que consiste en calentar la muestra de lodo hasta que se evaporen los componentes líquidos para luego pasar a través de un condensador. El líquido es recogido y medido en un cilindro graduado y el porcentaje de sólido, suspendido y disuelto, se obtienen por diferencia, es decir restándole a 100% el porcentaje líquido. En la Figura se visualizan los componentes de la retorta.
Con los resultados de una retorta se pueden hacer análisis de sólidos para conocer las lb/bbl de arcilla agregada y aportada por la formación, así como también la concentración de los sólidos indeseables incorporados al sistema. Para realizar este análisis es necesario conocer el peso del lodo, el porcentaje total de sólidos y el resultado de una prueba de azul de metileno (MBT). En consecuencia, el análisis de sólidos aplica sólo para los lodos base agua y no base aceite, debido a que a estos lodos no se le hace MBT.
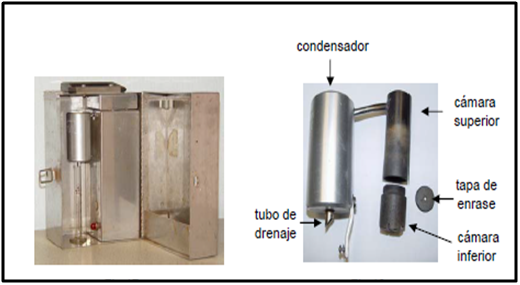
Componentes de una retorta.
*Tomado de Prieto (2007)*
La retorta es usada para determinar el contenido de líquidos y sólidos en el fluido de perforación. Los instrumentos de retorta recomendados son unidades con una capacidad de 10, 20 o 50 ml, con camisas externas de calentamiento. El fluido se coloca en un contenedor de acero y se calienta hasta que se evaporen los componentes líquidos. Los vapores pasan a través de un condensador y se recogen en un cilindro graduado. El volumen del líquido se mide, mientras que el contenido de sólidos, suspendidos y disueltos, se determina por diferencia.
Retorno de Permeabilidad
Este ensayo tiene por objetivo medir el daño causado por un fluido sobre la permeabilidad (k) de una formación productora. El ensayo se hace con varios núcleos y el procedimiento se lleva a cabo en tres fases: preparación del núcleo y medida de la permeabilidad inicial, exposición del núcleo al fluido de prueba, en medio de filtración dinámica o estática, cálculo del retorno de la permeabilidad.
La prueba de retorno de permeabilidad se usa para medir el efecto de un fluido de prueba (fluido completo, filtrado de fluido, o salmuera) sobre la permeabilidad de una formación productora. El ensayo utiliza testigos cortados de un núcleo de muestra, crudo y agua de formación del mismo yacimiento. La prueba consta de tres etapas:
Se mide la permeabilidad inicial (KI), del yacimiento circulando crudo a través del núcleo en la dirección de producción (Yacimiento a hoyo)
Se circula fluido de perforación/completación frente a la cara del pozo construyéndose un revoque en la cara de este (etapa de exposición). Se circula nuevamente crudo en dirección yacimiento pozo para determinar la permeabilidad del tapón afectado por el fluido (KF). Durante esta etapa se determina también la presión de levantamiento del revoque, la cual dará una idea de la facilidad de remoción de este.
Se determina el daño y la recuperación de permeabilidad como:
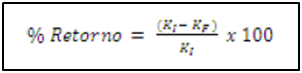
) (1)
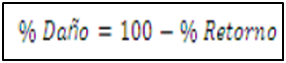
)(2)
Donde:
% Retorno: porcentaje de Fluido Retornando.
% Daño: porcentaje de daño del núcleo.
(KI) permeabilidad inicial
(KF) permeabilidad del tapón afectado por el fluido
Concentraciones Adecuadas del QC Drill Starch como Controlador de Filtrado en Fluidos de Perforación Base Agua Drill In en el Área de Zuata Principal
Es importante mencionar que, se prepararon muestras de fluido base agua Drill-In a razón de un barril de laboratorio, donde se emplearon productos químicos según formulación solicitada por la operadora, variando la concentración del aditivo QC Drill Starch estudiado para verificar y analizar los resultados de las propiedades físicas evaluadas según norma API 13B-1, con la finalidad de determinar la concentración adecuada.
Primeramente, se indican las cantidades de muestras que se evaluaron, para un total de 24, muestras tomando en cuenta la recomendación del fabricante de realizar las pruebas con una concentración inicial de 0,25 lpb y culminar con 6 lpb como concentración tope. A su vez, se detallan las concentraciones de cada uno de los aditivos que forman parte del fluido, incluyendo la función que cumple en éste, más la variación de concentración del producto químico QC Drill Starch para así evaluar su comportamiento.
A dichas muestras se le evaluaron propiedades físicas como la reología, filtrado API, filtrado AP-AT, potencial de Hidrogeno (pH), contenido de sólidosy líquidos para tomar estos resultados como referencia para continuar la investigación con aquellas muestras que cumplan con los rangos establecidos por la empresa operadora.
A continuación las concentraciones de cada una de las muestras:
Concentración de productos químicos para el fluido de perforación base agua Drill-In con QC Drill Starch. Muestras 1 y 2
Fuente: @barbieprzcdo
En el cuadro anterior se observan los productos químicos empleados para la formulación de las muestras 1 y 2 como el agua (fase continua/0.85 libras/galón), soda caustica (alcalinizante/0.50 libras/galón), goma xantica clarificada (viscosificante/2.0 libras/galón), acetato de potasio (inhibidor de arcilla/1 libras/galón), aceite mineral (lubricante/15 libras/galón), carbonato de calcio 40-45 (densificante-puenteante/15 libras/galón), carbonato de calcio 70-75 (densificante-puenteante/30 libras/galón) y carbonato de calcio 115-120 (densificante-puenteante/15 libras/galón) cuyos tiempos de mezcla fueron uno, dos, diez, siete, siete, cinco, cinco y cinco respectivamente. Variando la concentración del controlador de filtrado QC Drill Starch agregando 0.25 y 0.50 libras/galón para la primera y segunda respectivamente.
Concentración de productos químicos para el fluido de perforación base agua Drill-In con QC Drill Starch Muestras 3 y 4
Fuente: @barbieprzcdo
En dicho cuadro se observan los productos químicos empleados para la formulación de las muestras 3 y 4 como el agua (fase continua/0.85 libras/galón), soda caustica (alcalinizante/0.50 libras/galón), goma xantica clarificada (viscosificante/2.0 libras/galón), acetato de potasio (inhibidor de arcilla/1 libras/galón), aceite mineral (lubricante/15 libras/galón), carbonato de calcio 40-45 (densificante-puenteante/15 libras/galón), carbonato de calcio 70-75 (densificante-puenteante/30 libras/galón) y carbonato de calcio 115-120 (densificante-puenteante/15 libras/galón) manteniendo los mismos tiempos de mezclas. Del mismo modo variando la concentración del controlador de filtrado QC Drill Starch para la muestra tres de 0.75 libras/galón y cuatro 1 libras/galón.
Del mismo modo, en el proximo cuadro se observan los productos químicos empleados para la formulación de las muestras 5 y 6 como el agua (fase continua/0.85 libras/galón), soda caustica (alcalinizante/0.50 libras/galón), goma xantica clarificada (viscosificante/2.0 libras/galón), acetato de potasio (inhibidor de arcilla/1 libras/galón), aceite mineral (lubricante/15 libras/galón), carbonato de calcio 40-45 (densificante-puenteante/15 libras/galón), carbonato de calcio 70-75 (densificante-puenteante/30 libras/galón) y carbonato de calcio 115-120 (densificante-puenteante/15 libras/galón) manteniendo los mismos tiempos de mezclas. Del mismo modo variando la concentración del controlador de filtrado QC Drill Starch agregando 0.75 y 1 libras/galón para la quinta y sexta muestra del mismo modo.
Concentración de productos químicos para el fluido de perforación base agua Drill-In con QC Drill StarchMuestras 5 y 6
Fuente: @barbieprzcdo
Seguidamente, en el siguiente cuadro se observa la formulación de las muestras de la 7 a la 21 empleando como las anteriores agua (fase continua/0.85 libras/galón), soda caustica (alcalinizante/0.50 libras/galón), goma xantica clarificada (viscosificante/2.0 libras/galón), acetato de potasio (inhibidor de arcilla/1 libras/galón), aceite mineral (lubricante/15 libras/galón), carbonato de calcio 40-45 (densificante-puenteante/15 libras/galón), carbonato de calcio 70-75 (densificante-puenteante/30 libras/galón) y carbonato de calcio 115-120 (densificante-puenteante/15 libras/galón) manteniendo los mismos tiempos de mezclas. Del mismo modo variando la concentración del controlador de filtrado QC Drill Starch de 0.25 libras/galón desde 1.25 hasta 5.25 desde la séptima hasta la vigésima primera.
Concentración de productos químicos para el fluido de perforación base agua Drill-In con QC Drill StarchMuestras de la 7 a la 21
Fuente: @barbieprzcdo
Adicionalmente, en el siguiente cuadro se observan los productos químicos empleados para la formulación de las muestras 22, 23 y 24, agua (fase continua/0.85 libras/galón), soda caustica (alcalinizante/0.50 libras/galón), goma xantica clarificada (viscosificante/2.0 libras/galón), acetato de potasio (inhibidor de arcilla/1 libras/galón), aceite mineral (lubricante/15 libras/galón), carbonato de calcio 40-45 (densificante-puenteante/15 libras/galón), carbonato de calcio 70-75 (densificante-puenteante/30 libras/galón) y carbonato de calcio 115-120 (densificante-puenteante/15 libras/galón) manteniendo los mismos tiempos de mezclas. Del mismo modo variando la concentración del controlador de filtrado QC Drill Starch agregando 5.50, 5.75 y 6 libras/galón.
Concentración de productos químicos para el fluido de perforación base agua Drill-In con QC Drill StarchMuestras de la 7 a la 20
Fuente: @barbieprzcdo
En el mismo orden de ideas, las muestras anteriormente preparadas fueron sometidas a evaluación sin envejecimiento, según el tiempo y orden de agregado, basándose en la norma API 13B-1 para la elaboración de pruebas físico químicas a los fluidos de perforación base agua. Posteriormente, se procedió al análisis y descartarte las muestras que no cumplieron con los rangos de propiedades físico – químicas exigidas por la operadora. Seguidamente, se envejecieron a 280 ºF por 16 horas solo las que estuvieron dentro del rango.
A continuación se indica los rangos de las propiedades exigida por PETROMIRANDA, denotando los rangos mínimos y máximos respectivamente para gel inicial, a diez y treinta minutos respectivamente, viscosidad plástica, punto cedente, pH, sólidos y aceite según retorta, mención especial el valor máximo que debe regir durante las operaciones de perforación en la zona productora empleando fluidos Drill-In como es el filtrado API no sobrepasando los 5 cc/30 min.
Rango de propiedades fluido de perforación base agua Drill In.
Fuente: Petromiranda, S.A.
Referencias:
Bravo y Guerrero (2011). Artículo. Estratigrafía. Publicado en la revista Universidad del Mar. México. Disponible: https://ddd.uab.cat/pub/ tda/tda_a2014n20/tda_a2014n20p41.pdf. [Consulta: 2016, junio 7].
CIED (2012), Manual de fluidos de perforación del Centro Internacional de Educación
Halliburton (2011), Manual Práctica recomendada para Pruebas en Campo de Fluidos de Perforación Base Agua
Manual de Samán, Tecnología Integral en Petroleó, S.A. (2010)
Sigueme: @barbieprzcdo
Vota
Comenta
Thanks!!!
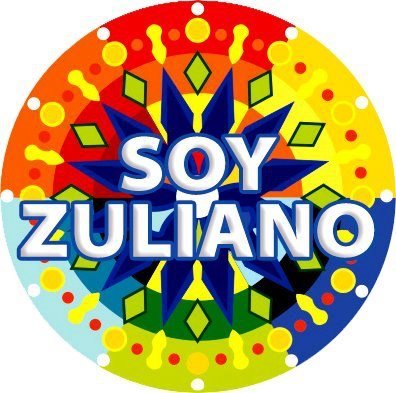