How To Make Stoneware Ceramic Using Locally Derived Raw Materials?
Slip casting is a great method for the mass-production of pottery. It is simply a forming technique for producing ceramic objects. It is especially useful for making complex forms that are non-concentric, irregular, square, and can also produce concentric forms. Slip casting is used to produce pottery, figures, sculpture, and sanitary ware.
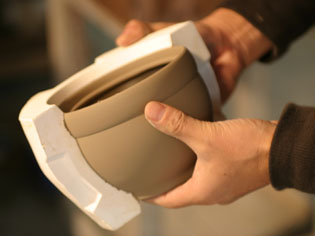
Liquefied clay (casting slip) is poured into a plaster mold. The plaster mold is absorbent and will begin to draw water from the casting slip. The longer the slip sits in the mold the more water is drawn from it by the mold and the thicker the casting becomes. A step by step process of the slip casting method with detailed discussions on results obtained from different tests involved in the process are also shown. However, it discusses only the implications of Maria Cristina clay formulation.
This also includes glazing of the casted ceramic body. 90% feldspar and 10% clay were used as a glaze composition. Glazes can be thought of as a glass coating, clear and transparent. They may also be glossy or matte, translucent or opaque, smooth or even textured. The effects are limitless depending on formulation, application and combinations.
Glaze can be applied in many ways. Common methods include dipping, spraying, pouring and brushing. The formulated glaze can be applied in microwavable cookware through dipping method.
I. Ceramic Slurry Preparation
The raw materials prepared were Silica, Feldspar and Maria Cristina clay. A ternary suspension composed of 70% solids and 30% water was made. For the water, 30% of the total batch weight was weighed and loaded in a bucket. Sodium silicate was added as deflocculant on the solid loading and mixed it together with the loaded water using the blunger. The ternary suspension was continuously stirred until all the solids are completely suspended and dispersed well with the liquid solution. Addition of the sodium silicate was poured with caution or else the amount of solids must be adjusted.
II. Specific Gravity
The specific gravity was determined after mixing the slurry well using the small cylindrical container. First, the dry and clean container was weighed and recorded. It was then filled with water and weighed again. This is the weight of water + weight of container. Next, the water was removed and the sample slip was poured until the brim was reached.
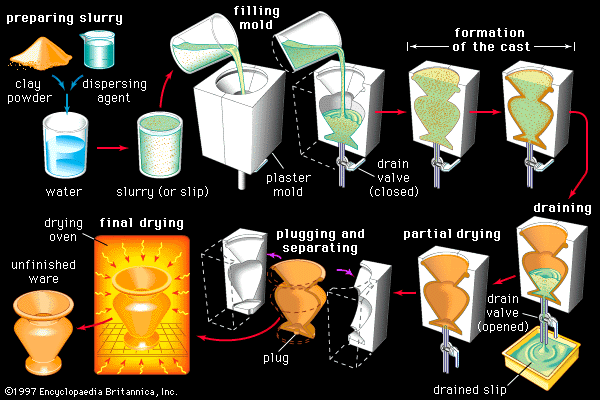
III. Ceramic Drain Casting
The casting slip was agitated first using the blunger for about a minute. Then the slip was slowly poured into the desired molder. The slip was sat still until the desired thickness was reached (about 3-5mm). Afterward, the excess slip was poured back into the container and the mold was left inverted to drain. The mold was turned over and sat for at least 1 hour or until firmed. Consequently the casting body was removed carefully. The cast body was set dried for a few hours until it is hard and dry. Next, it was fettled to trim off the unwanted parts of the clay. Later, the cast body was allowed to air dry at room temperature for 3-5 days. It was then oven dried at 60-110⁰C gradually increasing the temperature for 4 hours.
IV. Glaze Preparation
The raw materials composed of 10% clay and 90% feldspar and water was ball milled for 30 hours. A 90-10 composition was used because the glaze involved only two materials; clay and feldspar, and to attain a good glaze, the composition must fit into the oxide analysis of feldspar and clay. Thus, solving for the fit glaze of Maria Christina clay, a 90-10 composition would suffice. The ball milled sample was screened in 200 mesh to obtain fine particles. After screening, specific gravity was determined.
To form a good body using Maria Christina clay a tri-axial body with 20% Feldspar, 15% Silica, and 65% Clay with a slip that has a specific gravity of 1.8 grams per cubic meter. Results showed that a Maria Christina body had a total shrinkage of 2.8% and a Flexural Strength of 3.32 MPa thus following a pseudo-plastic behavior for a non-newtonian behavior of fluids. A good glaze, however, using Maria Christina clay must have a specific gravity of 1.4 grams per cubic meter. Linear coefficient of expansion also showed that the body and glaze calculation is compatible with a percent difference of 12.79% which can be found in the 5-15% range of acceptable difference in body-glaze system.
THANK YOU FOR READING MY POST!