Exploring the Versatility of Magnesite Ramming Mass: A Key to High-Performance Furnaces
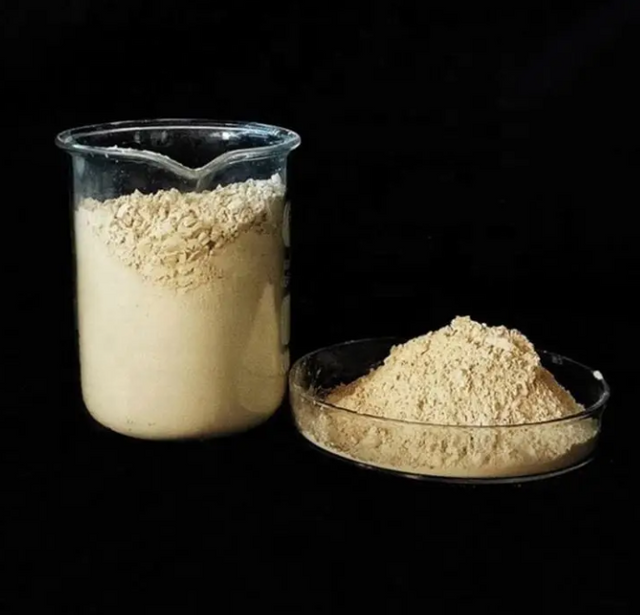
In the world of high-temperature industrial processes, magnesite ramming mass emerges as a silent hero. Often overshadowed by refractory bricks and castables, this material offers unique properties that make it indispensable for many applications. Let’s delve deeper into Magnesite Ramming Mass, exploring its versatility, significance, and the reasons it stands out in the realm of refractory materials.
What is Magnesite Ramming Mass?
Magnesite ramming mass is a refractory material primarily composed of dead-burnt magnesite. It is used as lining material in furnaces, providing excellent heat resistance and structural integrity under extreme temperatures. Unlike other refractory products, ramming mass is unshaped and is installed by ramming it into place, creating a seamless lining that adapts perfectly to the furnace's contours.
Why Choose Magnesite Ramming Mass?
To understand the importance of magnesite ramming mass, consider the challenges faced in high-temperature operations. From thermal shock and chemical corrosion to mechanical wear and tear, furnace linings endure constant stress. Magnesite ramming mass addresses these challenges effectively due to its:
-High Thermal Resistance: With a melting point exceeding 2800°C, magnesite ramming mass withstands intense heat without losing its integrity.
-Chemical Stability: Its excellent resistance to basic slags and corrosive environments ensures longer service life.
-Flexibility in Installation: Unlike pre-shaped bricks, magnesite ramming mass allows for customized applications, filling gaps and irregularities in furnace structures seamlessly.
Beyond the Basics: Applications That Shine
The versatility of magnesite ramming mass is evident in its diverse applications across industries:
1.Steel Industry: Used as lining material for induction furnaces, tundishes, and ladles, it helps maintain purity in molten steel and prevents contamination.
2.Non-Ferrous Metal Industry: Magnesite ramming mass finds use in furnaces processing aluminum, copper, and zinc due to its resistance to oxidation and chemical reactions.
3.Cement and Lime Kilns: It protects kiln linings from the corrosive effects of alkalis and other chemical compounds.
4.Glass Manufacturing: In glass furnaces, magnesite ramming mass resists the erosive action of molten glass, ensuring consistent production quality.
How Magnesite Ramming Mass Elevates Furnace Efficiency
While durability and resistance are key, the contribution of magnesite ramming mass to operational efficiency is often underestimated. Here’s how it makes a difference:
-Energy Savings: Its seamless lining minimizes heat loss, reducing energy consumption and improving furnace efficiency.
-Reduced Maintenance: With superior resistance to wear and corrosion, it extends the intervals between maintenance shutdowns.
-Improved Safety: A reliable furnace lining ensures stable operations, minimizing the risk of catastrophic failures.
Choosing the Right Supplier: A Crucial Step
The performance of magnesite ramming mass depends not only on its composition but also on the quality and consistency of the raw materials used. As a supplier, AGRM takes pride in offering magnesite ramming mass tailored to specific industrial needs. With ISO-certified manufacturing processes and a commitment to innovation, AGRM ensures that each batch meets the highest standards of performance and reliability.
Future Trends: What Lies Ahead for Magnesite Ramming Mass?
As industries strive for more sustainable and efficient practices, the role of magnesite ramming mass is evolving. Innovations in raw material sourcing and manufacturing techniques are expected to enhance its properties, making it even more versatile. Additionally, the focus on recycling and reusing refractory materials aligns with global efforts toward environmental responsibility.