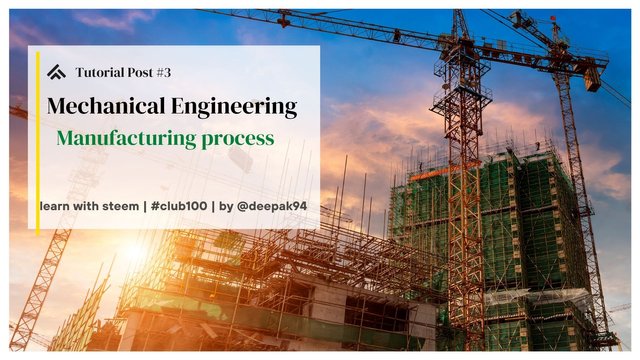
source-canvas
Namaste Steem Family, and my greetings to all my steemit friends and students who attend my lessons and learn about Manufacturing process.
During the last lesson, we learned about Rolling in Manufacturing process. Today, we are going to cover the rest of the process in this lesson. Now let us get started.
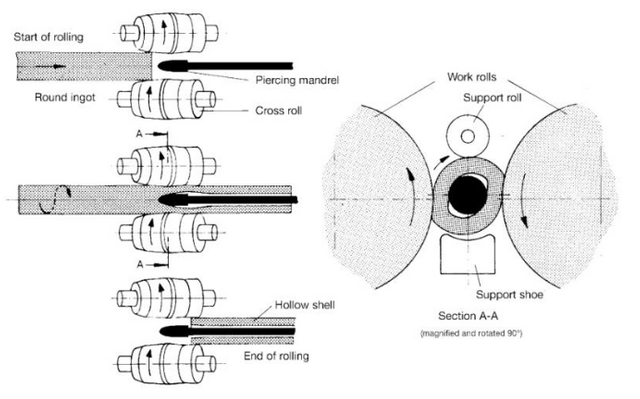
Source:
- Thick-walled and seamless tubing is made by piercing.
- Heated form of round billet leading and center punched, pushed longitudinal into two large and convex tapered rolls revolve in the same directions.
- Their axes inclined at opposite angle about 6 degree from the axis of the billet.
- The clearance between the roles is less than the diameter of the billet.
- As the billet is caught by the roll and rotated their inclination causes the billet to be drawn between them.
- The tube is then passed between reeler and seizing roles to straighten it and bring it to the desired size.
- The process is used to produce tubing up to about 30cms in diameter.
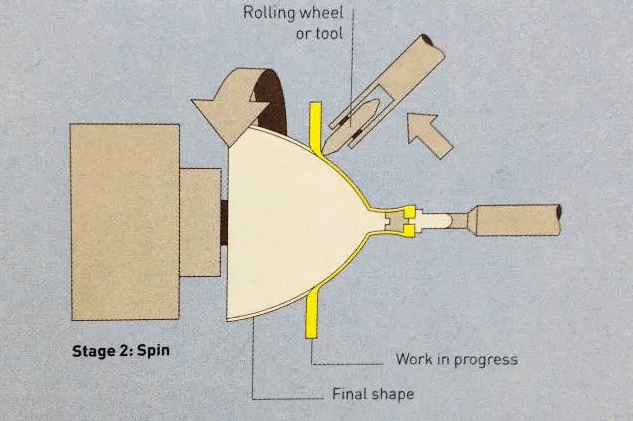
Source:
- Spinning is a cold working as well as a hot working operation.
- A rotating disk of sheet metal is drawn over a male form.
- outside of the disk applying a localized pressure.
- By means of a simple round-ended wood or metal tool or by a small roller.
- Spinning is economical for small-lot production.
- Bowls, lamp reflectors, cooking utensils and the bells of musical instrument are made from spinning.
- Some hot spinning is done to form thicker plates of steel into dished pressure vessel and tank heads.
- It is possible to form greater thickness of metal, without causing strain hardening by hot spinning.
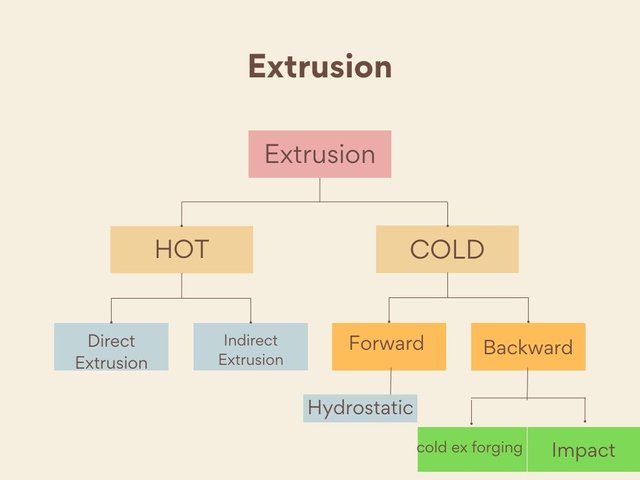

What is Extrusion
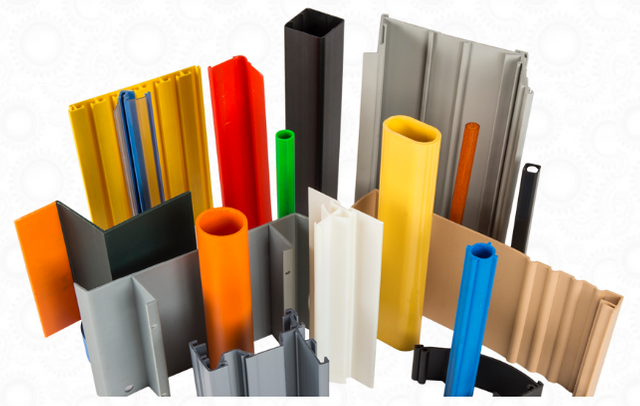
Source: PLASTIC Extruded materials
- Extrusion is more widely used in fabricating non ferrous metal and their alloys.
- Steel and other ferrous alloy can also be successful processed.
- Rods from 5mm to 200mm in diameter can be extruded.
- Tubing with an inside diameter up to 800 mm and a wall thickness from 1.5 to 8 mm can be extruded.
- Ratio of the cross section area of the billet to the cross-sectional area of the product.
- About 40:1 for hot extrusion of steel
- 400:1 for Aluminum.
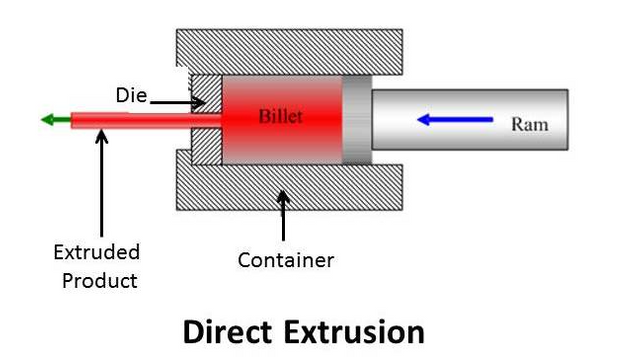
Source:
A solid ramp drives the entire billet to and through a stationary die and must provide additional power to overcome the frictional resistance between the surface of the moving billet and the confining chamber.
- Hot extrusion involves temperature of 500 to 1200 degrees Celsius depending on the work material extruded, the cylinder and ram are severally affected by the temperature. As well as stresses.
- The pressure applied from 35 to 100Mpa. The extrusion process for a given material depends on the extrusion temperature, the reduction in area and the extrusion speed.
- The extrusion speed of the light alloy is maybe 0.5m/sec.
- For the copper alloy it is may be as high as 4.5m/sec.
- Scrap indirect extrusion is 18 to 20% of the billet weight.
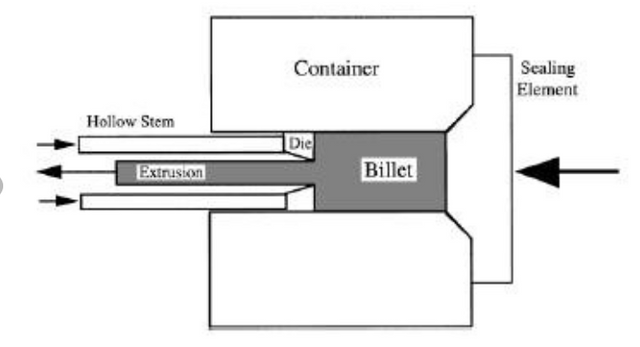
Source:
- Through a stationary confined billet. A Hollow ram drives the die back .
- If no relative motion, the friction between the billet and the chamber is eliminated.
- Required forces lower (25 to 30% less)
- Low process waste only 5 to 6% of the bullet weight(scrap).
- Used with a low-strength metals such as zinc, lead, tin and aluminium to produce collapsible tubes for toothpaste which is used in our daily life, medications, and other creams; small "Cans" for shielding electronic components and large cans for food and beverages.
- Now-a-days forming is used for mild steel parts.
- From the non ferrous metals any cross-sectional shape can be exctruded.
- Many shapes(than rolling).
- No draft.
- huge reduction in cross sections.
- only single die change requires for Conversion from one product to another .
- Good dimensional precision.
for the entire length of the product cross section must be uniform.
Lubrications for extrusion |
- For hot extrusion glass is an excellent lubricant with steel, stainless steel and high temperature metal and alloys.
For cold extrusion, lubrication is critical, especially with steels, because of the possibility of sticking(seizure) between the work-piece and the tooling if the lubricantion breakdown. The Most effective lubricant is the phosphate conversion coating on the workpiece.
Today in entire topic we learn about different mechanical deforming process in which we learn about spinning, piercing and Extrusion process. We learn about the advantage of extrusion process and limitations.

I hope you liked this tutorial series of mechanical engineering subject and please tell me in the comments, what you liked in this tutorial.

Thank you
Thank you for contributing to #LearnWithSteem theme. This post has been upvoted by @cryptogecko using @steemcurator09 account. We encourage you to keep publishing quality and original content in the Steemit ecosystem to earn support for your content.
Regards,
Team #Sevengers
concept bhut accha hai aapke post ka
tutorial is difficult for me if you allow to I can share related to medical field